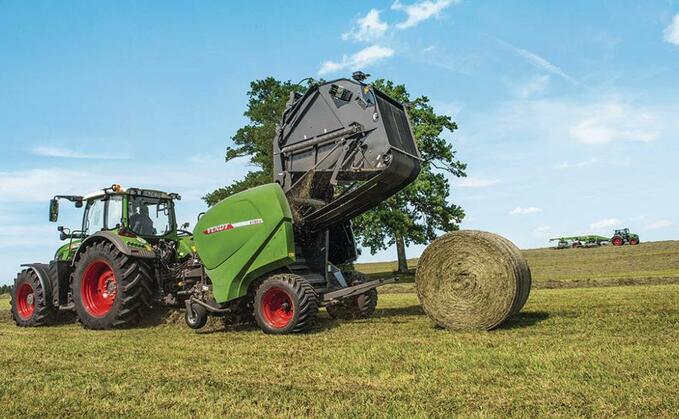
The pressure is on as baling gets underway, but extra attention to set-up, baling and wrapping technique, and care of net and plastic can make all the difference to bale quality.
Many factors come into making the perfect round bale, several of which can be tackled before the baler even rolls in the field.
Ground conditions, mowing technique, swath shape and baler set-up all play their part in making good bales.
The wet spring means many grass fields are rough this year, and the mower should be set accordingly, says Dan Woodward, Fendt forage products specialist.
"Operators should be aiming to leave a greater stubble height, ideally about 10cm.
"Then you can adjust the support chains on the baler pick-up to lift its working height and avoid gathering soil or debris into the bale."
Once mown, swath presentation is key to making well-shaped bales, suggests Mr Woodward.
"You need a good twin-rotor rake, or a very competent operator on a single-rotor rake, to produce a nice box-shaped swath, which helps to give a good edge to the bale."
If a consistent box-shaped swath cannot be achieved, baler driving technique can also affect bale shape. Again, aim for consistency, says Mr Woodward.
"If baling a narrow row you may need to weave slightly, 40cm to the left, then 40cm to the right to give a good edge to the bale. Speed is down to the conditions, but working slower reduces wear and tear on the baler - about 12kph is the aim."
The choice of a fixed or variable chamber baler depends on the owner's workload and whether the focus is on silage, hay or straw, but Mr Woodward points out variable chamber balers are now better able to make high quality silage bales given a good swath.
"In more variable conditions, a fixed chamber baler may be better as it is effectively a big tumble dryer and can cope with lumpy swaths."
WRAPPING
Whether wrapping with a combi system or separate wrapper it is important to ensure sufficient layers are applied to the bale to prevent air getting in.
The ideal number is always up for debate, but Ibers silage specialist Rhun Fychan suggests a minimum of six layers, despite the extra cost and disposal issues.
"It is the best way to ensure quality. The more layers, the less risk of air getting in," he says. "It is particularly important if bales are wrapped in the field rather than at the stack, because more layers minimise the risk of damage as they are loaded and transported."
He suggests operators should take care to avoid dropping bales onto hard stubble if only using four layers, as trials showed they were more prone to ‘pinpoint' damage, which leads to the development of moulds.
Using film in the bale chamber to wrap the circumference of the bale instead of net is a facility offered on a growing number of balers, and Mr Fychan says while it is a good idea in principle, as it can offer more protection to the bale, the plastic does not cover the shoulders of the bale.
"This is the area where bales tend to get damaged, so if using film-on-film, remember it is not a replacement for traditional film wrapping, but an addition, so you will still need six layers rather than reducing to four."
Using more film means more to dispose of and Mr Fychan says plastic should be collected and taken to an undercover storage area as soon as it is removed.
"We have seen water gets between the layers, so once it is wet, it is hard to dry, with the water adding to the weight and thus to disposal costs.
Graham Robson says: "When wrapping with black film, it is impossible to see how accurately your wrapper is at overlapping it. Unlike white or green film, you will never see the overlap pattern. To check, turn the bale on end, cut around the base and lift the wrap off the bale. Climb inside the film taken from the bale and look for areas with fewer layers, which will be easy to see."
On the wrapper, check the knives from time to time to ensure they are still sharp. Blunt knives can snag wrap, wasting plastic, causing downtime and preventing the plastic from sealing properly.
Mr Robson says: "The film must be released by the catch and cut mechanism at the start of the new wrapping cycle. If the knife is not sharp enough, broken or misaligned and the film does not release, it will allow air into the end of the bale, between the film layers, resulting in poor quality silage.
"Also, as the bale rolls away it pulls the film away, reducing the number of wraps left on the bale."
Aim to collect bales and stack promptly, as birds landing on the bales in the field will puncture the film and make larger holes as they pull the grass through, causing moulds from the air which can now enter the bale.
"It is a waste of time, effort and expense," says Mr Robson.
"Far better to plan some time into the day to get the bales cleared and stacked."
GETTING THE BEST FROM NETWRAP
THE GOOD
It is easy to neglect machinery in a busy season, but poor baler condition can affect the way it feeds netwrap, leading to annoying downtime.
Netwrap snagging, sticking and failing to cover the bale properly is frustrating but can be avoided, suggests Graham Robson, technical manager of Tama UAT.
"Anywhere the net is in contact with metal should be clean and free from dirt or rust. You can check for rough edges with a nylon stocking. If the stocking snags, then it is a good bet the net will too. Use a pan scrub to rub it smooth."
It is important to check the performance of the net rollers too, he says.
"If the net feeds in by powered feeding rollers, they must be adjusted correctly to give a uniform ‘pull' across the net's entire width when feeding."
Completed bales can be damaged if they are held in the chamber when they should be ejected, as the continued rotation of the bales damages the net.
"Rust from a baler which has been stored or even paint on a new baler can slow the bale's rotation," says Mr Robson.
"This can be resolved by disengaging the pto before ejecting the bale, until the side walls are made shiny by repeated contact with grass."
THE BAD
Stones or broken tines which get picked up by the baler will damage the surface of the rollers, causing net to snag and tear or pulling it off the bale surface, where it can wrap round the rollers.
"Check the rollers carefully after working in a stony field or if a pick-up tine has broken."
The condition of the netwrap is also significant. Check your netwrap rolls if you have been caught in a downpour or rainwater has got into the storage shed.
"If the netwrap system works against the core of the roll, it is important the core remains dry," says Mr Robson.
"In New Holland, Krone and Welger [now also sold as Fendt/Massey Ferguson] balers, net tension is created by holding the roll against the braking action, using teeth on the shaft which goes through the roll. If the core is wet, the teeth cannot grip the inner core, so will not achieve the required tension."
Ensure the net actually wraps around the bale. If the bale continues to form once the netwrap begins to feed, it will get embedded inside the crop.
"The netwrap should always be on the outside of the bale, otherwise it cannot fully hold the crop," says Mr Robson. The bale will swell and probably burst, either due to the outer layer being damaged, or from the lack of layers on the outside not being sufficient to contain it.
"The solution is to stop driving when the net begins to feed. Otherwise the bale continues being formed and the net ends up embedded inside the crop."
When you start baling, check the netwrap coverage. It is generally designed so the threads cover the curved surface of the bale only. If it overlaps the sides, this reduces the holding force of the threads.
THE UGLY
"If a net has 50 threads and three are over each side (i.e. six ‘lost' in total from 50), this means the net has lost 12 per cent of its ‘holding force'," he says.
However, the net must also cover the shoulders, or air can be trapped when the bale is wrapped, leading to mould growth spoilage.
"Also, the uncovered ‘shoulders' on the bale can puncture the film when the bale is being wrapped, creating more places for air to get into the bale, making the situation worse."
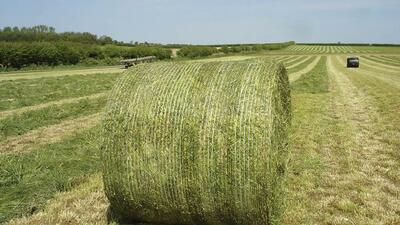
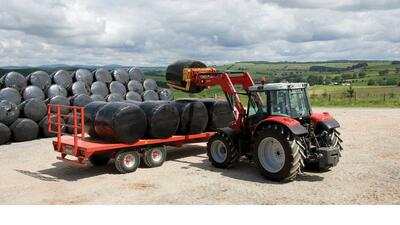