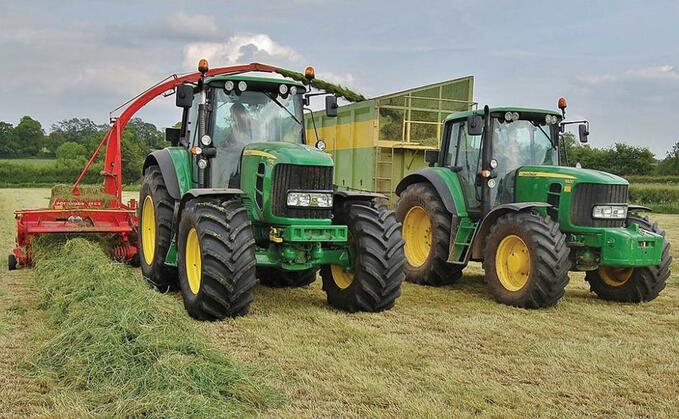
The trailed forage harvester has virtually been relegated into obscurity, yet for many livestock farmers, it still represents a solution to finding a manageable alternative to using a contractor with a high-output self-propelled machine.
Simon Henley reports...
Thirty years ago, the trailed forage harvester was at the forefront of silage production in the UK and Ireland.
Major manufacturers, such as John Deere, New Holland and Massey Ferguson, all offered precision-chop trailed machines, which competed in the UK market with popular European brands, such as Claas, Reco-Mengele, Krone and Taarup.
With the passage of time, the popularity of the trailed forage harvester dwindled significantly, as contractors strived for greater harvesting capacity and higher working outputs.
Today, there are essentially only three major players in the UK trailed forage harvester market, including the JF Stoll (Kongskilde), Pottinger and Agco/Lely.
The trailed machine quickly became outclassed and out-performed by the self-propelled forage harvester, a machine which continues to play a key role in silage production on UK farms.
Uses
In addition, the uses of forage wagons has also grown, popular for their alternative chopping style, reduced labour and overall running cost requirements. However, both of these ‘newer' systems are not for everyone.
Although the self-propelled does offer a very efficient way of getting grass from field to clamp, some farmers feel the high-output harvesting process has come at the detriment of producing quality silage.
For those livestock and dairy farmers who prefer to take a hands-on approach to producing their own high-quality silage, the trailed forage harvester remains a capable machine.
LITTLE AND OFTEN MORE DESIRABLE
David Luxton is a farmer from Bradworthy, Devon, who farms 141 hectares (350 acres) with his partner Sarah and her parents Rob and Elizabeth Haworth. This is a traditional Devon dairy farm with a herd of 200 cows.
Mr Luxton, who operates a John Deere 3765 trailed harvester, says: "We live in an inherently wet climate.
To use a contractor with a self-propelled machine, we would need to drop 100 acres in one go, which we do not want to do.
"Our goal is to harvest little and often, starting with the first cut during the first week of May."
Using a trailed machine, Mr Luxton cuts lighter crops with a lower yield to achieve a high-quality silage with a metabolisable energy rating of 11.5MJ.
Typically, at peak season, he harvests in the region of 15-20ha (37-50 acres) per day.
Cutting
He says: "We will make up to four cuts per season, without risk of compromising nutritional value of grass. This is only achievable with careful grassland management, and using a trailed machine gives us this flexibility."
Mr Luxton has a preference for using older John Deere harvesters, which can be purchased and maintained at relatively low cost, albeit with the compromise of limited output.
RELIABILITY A PRIORITY
Alan Barlow works for R.J. Smith and Son, Rugeley, Staffordshire.
He operates the farm's 2006 Pottinger Mex VI flywheel forage harvester, which is used behind a 210hp New Holland T7060 to harvest 160 hectares (400 acres) of grass taken in two cuts at an average rate of 20ha/day (50 acres).
With 200 cows to feed, silage quality and improved grassland management are once again cited as being fundamental reasons for employing a trailed harvester. Another factor is R.J. Smith and Son also grows potato.
Grass leys for silage and grazing are sown following a potato crop. The process of destoning during potato planting inherently leaves a higher concentration of stones in specific areas of the field, making rolling an essential element of the pre-harvesting routine.
Mr Barlow, who has been driving trailed foragers for 20 years, says: "I prefer flywheel type machines. A large stone passing through the cutting drum on a JF harvester can literally obliterate the knives.
"On a flywheel machine, such as the Mex VI, the damage is restricted, downtime is reduced and the cost of repair is significantly less.
"The important thing on the Mex VI is to keep the blower paddles in good order. We remove them and reshape them every couple of years. It is essentially a one-day task, but is essential for maintaining wind speed in the spout.
"If there is a weak point on the Mex VI, it is the V-belt which drives the intake auger and feed rollers.
On six-metre windrows, even with 200hp on the front, it will not let you push it on. It is about maintaining a steady pace to achieve the best results.
"The benefit here is the V-belt protects the driveline. These days can buy the belts for less than £50. We generally replace two belts per season, but this will increase if you have choppy or bulky windrows. A good man on the rake is a necessity."
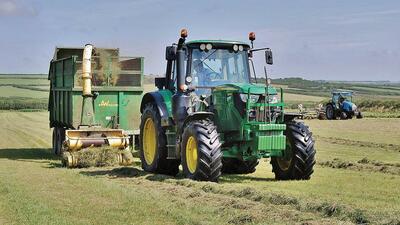
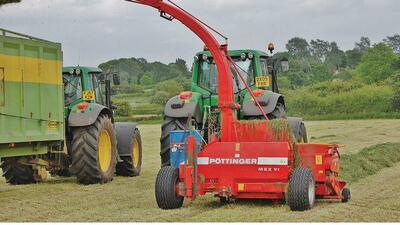
Trailed forager pros and cons
With the decline in the number of mid-sized livestock and mixed farms in the UK, it is unlikely the trailed forage harvester will make a prolific comeback.
For the large-scale contractor, who follows the grass harvesting season with maize harvesting, the self-propelled machine is a must.
Trailed machines simply do not have the capacity to economically deal with large acreages of maize.
In reality, trailed forage harvesters are not for everyone. Without careful management, such as harrowing and rolling grass fields in spring to remove stones and debris (in addition to careful disposal of fencing wire), stoppages and breakdowns can quickly become a nightmare.
Additionally, multiple cuts require the silage clamp to be re-opened and resealed. This, in itself, is a laborious task which can be time-consuming.
On the plus side, trailed machines are relatively cheap to buy on the second-hand market, they do not take up much room in the back of the shed and the tractor used to drive them can be put to work on another task.
But there is something else to consider which is more important. The benefit of using a trailed forage harvester, primarily equates to the quality of fodder being produced.
Improvements in feed management technology have enabled farmers to more precisely manage feed rations necessary to optimise milk and meat production.
Having the flexibility to harvest grass for fodder, at precisely the right time in manageable quantities, requires a flexible and affordable harvesting solution. For the mid-sized farmer, the trailed forage harvester is one such solution.