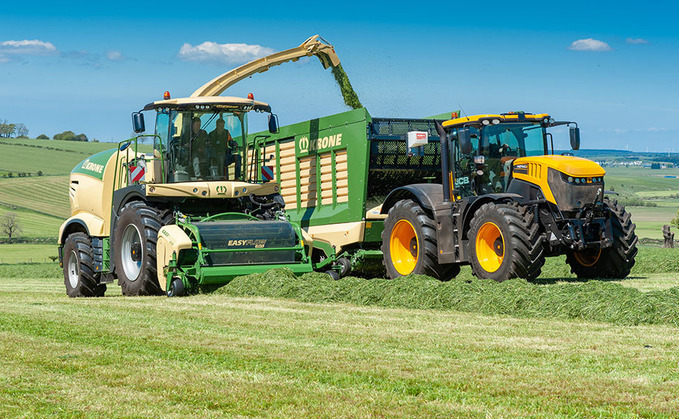
Famous for its range of high-powered, self-propelled forage harvesters, Krone is on a mission to emphasise that it takes more than just shear brute force and ignorance to chop grass well.
James Rickard reports from a very sunny Scotland. Pictures by John Eveson.
Pick-ups, feed rollers, chopping cylinder, accelerator. You will find all of these major crop-engaging elements in every self-propelled forage harvester make in the world, but like many things, it is what you do with them that counts.
It is a point not lost on German maker Krone, with its range of BigX choppers. Still a relative newbie to the market, especially when you consider how long the likes of Claas and New Holland have been on the job, it reckons it has hit on the ideal formula of component layout and design.
More importantly, it says its foragers have not just been designed with maize in mind, as several of its innovations point toward. James Duggleby, Krone UK product marketing manager, explains; "We have been on the forager market now for 19 years, and in that time we have gained a reputation for high capacity machines.
"However, we have also learnt a lot, with several innovations introduced over the years, much of which makes a massive difference in grass. To recognise this culmination of forager developments and knowledge, we have created the term OptiGrass."
And when you consider that grass is still the largest forage crop in the UK, approximately 11,200 hectares in total grass area, it is an important acknowledgement.
To find out more about ‘OptiGrass' and where the manufacturer is up to in terms of its grass handling capabilities, we headed to a rather hot Scotland and put two of its BigX choppers to work.
Now boasting a family of eight foragers, the range comprises four narrow body machines with a 630mm crop channel, and four wide body machines with an 800mm crop channel (see BigX range overview panel).
As previously explored with the launches of its narrow body machines and its newest, and fourth generation wide-body machines, all models share the latest family styling as well as a whole host of other goodies. This extends to an all new cab, the addition of independent rear wheel suspension, new roller frame attachment system, use of adaptive eccentrically-mounted wheel motors, improved crop processor changeover, flexible tank options and improved storage.
Our weapons of choice for the day was a model from its narrow body range, the BigX 580, and one from its wide-body line-up, the BigX 680.
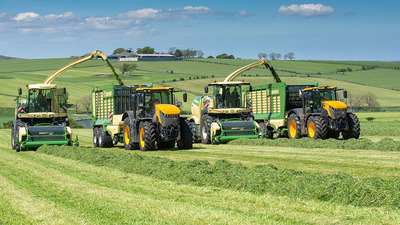
Pick-up
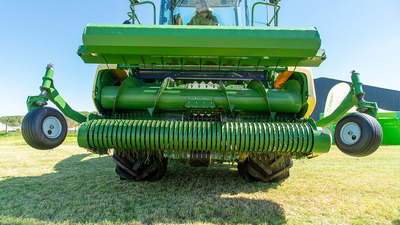
First up in the BigX's armoury of grass handing elements is its EasyFlow header. Unlike all of its competitors, it is the only header on the market to use a cam-less pickup, as opposed to moving tine bars running in a cam track.
It is a subject which firmly splits opinion as to which method is better. From an operator's point of view, the fewer moving parts, and therefore less maintenance, will be appealing. As too will be its sweeping action which is less prone to stone pick-up, and the ability for the manufacturer to configure its five rows of pick-up tines in a ‘W' configuration which helps spread the crop across the width of the pick-up.
Some operators may miss the more positive action that a cam-track style pick-up might offer, along with what could be perceived as a more controlled transfer of crop to the auger, rather than simply relying on speed, but it is hard to deny the EasyFlow pick-up does a good job.
Helping its cause is the ability to independently vary speed of the pick-up from 350 to 700rpm, adjusted hydraulically from the cab. It means, and as we found on the day, you can tailor the pick-up speed to the crop conditions.
As well as being able to do this manually, it can also be run in SynchroSpeed mode, which automatically adjusts pick-up speed based on forward speed - this can be further fine-tuned to suit.
Ground following
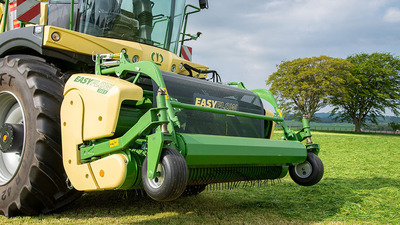
One of the key elements in avoiding crop contamination is decent ground following, of which the header has several tricks up its sleeve. In the first instance is the use of three ground following wheels; one jockey wheel either side of the header and a third wheel in the middle underneath, giving a stable triangular pattern.
Nothing revolutionary about that you might think, but the infinitely variable height adjustment of the jockey wheels is a neat touch, facilitated by a screw thread. It means you can find that ‘just right' height and not be limited to a pre-set pin and hole adjustment.
In addition, the header is mounted via a pendulum frame to the forager, which affords four-degrees of lateral tilt.
Feed rollers
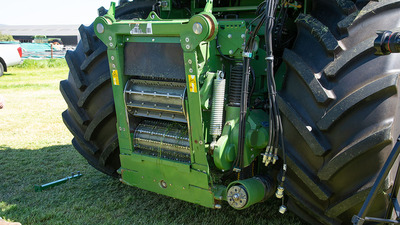
Compressing and transferring grass from the header to the chopping cylinder is a set of six feed rollers on the BigX; three at the top and three at the bottom. Krone, along with Fendt, are the only two forager manufacturers to do so, and as we have found, it seems to make a lot of sense.
While it is up for debate as to whether six feed rollers actually provide any more compression than four, it does seem that six rollers do offer a more controlled feed of grass to the chopping cylinder, presenting a more gradual and even-shaped wedge of crop. At the rear roller, up to five tonnes of pressure can be applied.
Six feed rollers have a further advantage, when it comes to providing protection to both the forager and the cows' stomachs. Like most foragers, BigXs are fitted with metal detectors and ‘rock stoppers,' and like all detection systems they need a chance to work if they detect a foreign object. As such, the 820mm distance from the front of the six feed rollers to the chopping cylinder, provides that little bit of extra stopping distance, compared to four.
Feed rollers are hydraulically driven, allowing chop lengths to be adjusted on the go. You can also pre-set two chop lengths which you can flick between, so no excuses for not adapting to dry matter levels.
Chop length adjustment can also be tied into the firm's spout-mounted crop sensor, which will automatically alter chop length based on dry matter.
Chopping cylinder
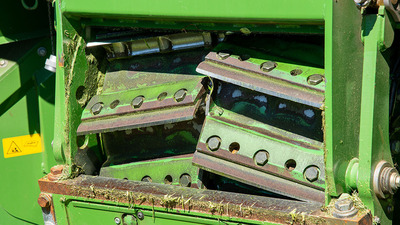
Latest developments to the forager's chopping element was the introduction of the MaxFlow chopping cylinder in 2015.
A key difference to its predecessor is that its blades are mounted underneath the blade holders, providing twice the crop carrying capacity while keeping crop away from the blade holders, improving wear and tear to the cylinder. Even with this set-up, blades still have a little ‘give', and can be knocked back in case they strike an object. And to make resetting them and fitting them easier, eccentric cam nuts are used to get the knives into position.
Blade angle and layout has also been thought about, which sees a chevron blade pattern employed with an 11 degree blade angle. This results in constant blade contact with the shearbar, and smoother running, says Krone. Weighing in at approximately 600kg (depending on number of blades fitted), the 660mm diameter cylinder also has plenty of inertia to absorb varying loads.
Blade options include 20 (offering a 5-31mm chop length), 28 (4-22mm) or 36 (3-17mm). A 40-blade biogas-spec cylinder can also be specified, and for extra flexibility, half sets of blades can be used with blanks in place of the removed blades, to protect the blade holders. The manufacturer says, a complete drum can be interchanged within an hour, gearing the forager up for maze.
Access and maintenance
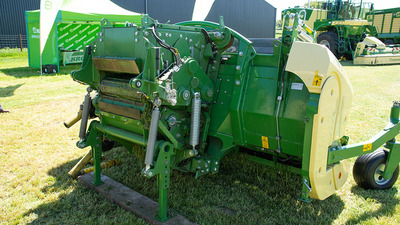
Access to the chopping cylinder can be done in one of three ways; leave the feed rollers attached to the header and ‘crack' open the rollers away from the cylinder to allow partial access; leave the feed rollers attached to the header and completely disconnect and drop off the feed rollers away from the chopping cylinder housing; or drop the header off then drop the feed rollers onto the trolley.
As we found in the field, the middle one is perfectly doable, though Claas' Jaguar 900 access and JD's latest forager access is hard to beat.
A recent addition to the forager is auto-shearbar adjustment, via the use of a single ‘knock sensor'. So rather than having to get out and adjust the shearbar manually, the new system can do it all for you. This neatly complements a system the manufacturer has had for a while, which sees the concave automatically adjust as the shearbar is adjusted via a mechanical linkage - this definitely saves an awkward job.
Crop channel
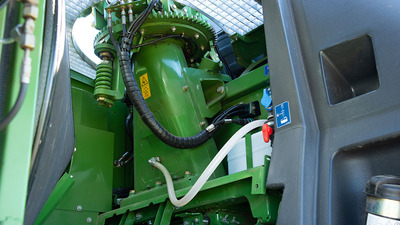
Introduced in 2009, one of the most satisfying elements of the Krone forager, particularly if you ask an operator what a Krone forager is like in a lumpy swaths, is the use of the firm's VariStream system.
It essentially comprises a sprung-loaded drum bottom and a sprung-loaded accelerator back plate, providing the ability to handle variations in crop flow. This in turn helps to take away peak loads away from the engine, which in turn protects the driveline. It also allows the engine to run at a more constant rpm, helping to provide a more consistent chop length. In our tricky conditions, you would have really missed this feature if it was not there.
Complimenting this is StreamControl, introduced in 2015, which allows adjustment of the accelerator back plate, enabling material to be blown further. One of three positions can be selected, which vary how much the accelerator paddles engage with the crop - the more they engage, the more blowing force they provide. When trailers are running alongside, the least aggressive setting is ideal, for opening up a field of maize, for instance, when a trailer is running behind, then the max setting would be the one. However, the more the paddles that are engaged, the more fuel you will use.
BigX range overview
Model | Maximum power | Engine | Chopping cylinder width/crop channel |
12.8-litre, S6, MTU | |||
12.8-litre, S6, MTU | |||
15.6-litre, S6, MTU | |||
15.6-litre, S6, MTU | |||
16.16-litre, V8, Liebherr | |||
16.16-litre, V8, Liebherr | |||
16.16-litre, V8, Liebherr | |||
1,156hp | 24.24-litre, V12, Liebherr |
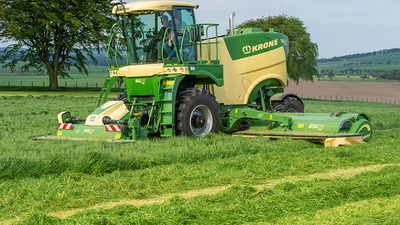
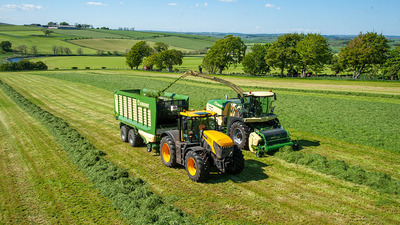
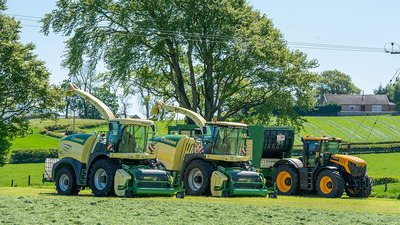
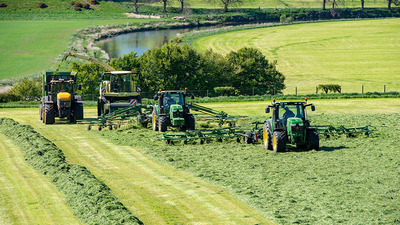