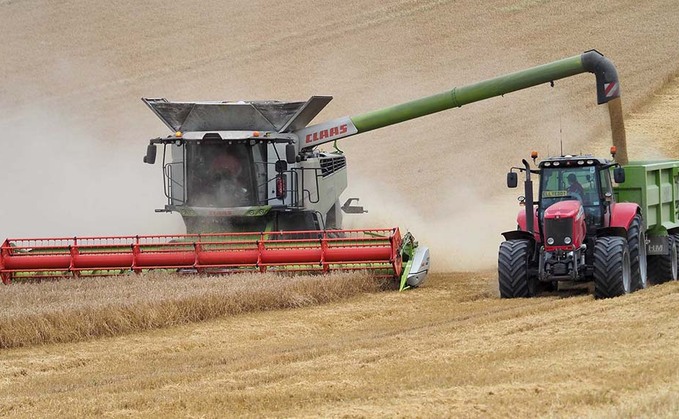
When Claas added its latest harvesting technology to the straw walker Lexions, a Cambridgeshire farm was keen to try a pre-series model. Jane Carley reports.
Updating a combine presents an opportunity to take advantage of the latest in technology and increase performance, even when requirements have not changed.
Wilbraham Farms, Cambridgeshire, harvests 1,000 hectares of cereals each year, on owned and contract farmed land, mainly malting barley, feed wheat and peas.
The large fields some are 50-60ha are mainly flat, and along with block cropping this helps boost work rates, but as farm manager Chris Ascroft explains, a policy to simplify operations is a factor in combine choice.
He says: We work as a team of two full-time plus two harvest operators, and the focus is very much on conserving moisture on our light land as the season progresses, aiming to plough, press and drill in a tight timescale. We are also split 50/50 autumn and spring crops, which spreads the workload.
In 2020, the farms seven-year-old Claas Lexion 670 came up for replacement and the manufacturer offered a pre-series machine for its new Lexion 6900TT, at a similar capacity and size.
Mr Ascroft says: We did have a New Holland CR9.90 on demo and it came very close, but Claas was able to offer a competitive price and there is the benefit of the company and dealer, Manns, being just down the road.
Combine output is specified to match the business single tractor and trailer carting policy.
As part of the lean operation, an 18-tonne trailer is hired in for the harvest period from manufacturer HM Trailers and towed by the farms MF7499, driven by a seasonal operator.
Mr Ascroft says: It allows us to comply with the important requirements for road safety by using the very latest, high specification trailer. Actually, the 6900TT could almost do with one-and-a-quarter trailers.
The combine was also specified with the same 9.3-metre-wide Vario header as its predecessor, rather than the recommended 10.8m version.
Mr Ascroft says: It is easy to change fields without taking the header off with a smaller width and it is quite adequate. We did look at the Convio, but reckoned it was not necessary for most of the fields as they are so flat. In wet conditions our soil can get very soft and the barley heads bend on the soft straw, so the ability to tilt the Vario back is useful.
Tracked combines have been used on the farm for 15 years; Mr Ascroft says while ruts are no smaller in wet conditions, compaction is less dense. The latest models also have top speed of 40kph, he says. The man at the helm of the combine come harvest is operator Jim Morris.
He says: There is a big difference on the road between a machine on wide tyres and one on tracks. The reduced width makes navigating villages easier and there is also a health and safety aspect. If you hit a pothole on big tyres, it is hard to bring the combine under control again quickly.
Claas has made a number of updates to this series, including a new level of automation with Cemos Auto Threshing, which uses readings from the grain quality camera and Quantimeter yield measuring system to automatically adjust concave settings and drum speed. Cemos Auto Cleaning tweaks the Jetstream fan speed and sieve settings to fine-tune operations according to changing conditions.
Mr Ascroft says: It is the best sample I have seen. We have achieved very high quality for malting with low nitrogen and low screenings and small grain.
Mr Morris agrees: The grain is exceptionally clean. The system is constantly making adjustments and you have to learn to trust it. An operator would not have the time nor inclination to be switching drum speed and concave settings when opening up the field, but the system just does it for you.
Grain camera footage is displayed on the CEBIS monitor, allowing the operator to override the system and make fine adjustments to settings based on factors such as broken grains.
Mr Morris says: I can also optimise the Cemos Auto Threshing according to our requirements and the conditions. In good conditions I can prioritise grain quality, but if the weather looks to be deteriorating, switching to increase output is achieved at two taps of the screen. It looks complicated, but it is actually very intuitive.
Swapping between crops is also automated by selecting the crop to be harvested on a drop-down menu, concave settings are adjusted hydraulically to suit.
Telematics further automates the harvesting operation sharing A-B lines with the carting tractor, and developments to the yield mapping show variations in detail. Yield maps and field records are automatically transferred to the farm office as each field is completed.
A change to unloading auger operation keeps the cross auger going once the grain tank is unloaded to completely empty the tube, avoiding grain loss into the field.
Mr Morris highlights another neat development paddles on the light brackets either side of the chopper sense the wind direction and adjust the power spreader and deflector to prevent residues blowing back into the crop.
Mr Ascroft says they are still scratching the surface of what the combine can do.
He says: I did not drive it at all last season as we were sticking to separate machines due to Covid-19 and yields were so poor that it was not a true reflection of what it could achieve. We are seeing more this year, but again yields are just 5.5-6t/ha in winter barley, so it is not working in big crops.
Conditions have also been testing this year, from unpredictable rainfall to a sudden hailstorm which took pea yields from 1.7t/ha to 0.7t/ha.
Mr Ascroft says: These were peas being grown for seed and the short crop was decimated by the hail.
Second wheats for a neighbour were also a low yielding, undemanding crop to harvest.
However, Mr Ascroft says the benefits of Claas updates are being seen already.
The APS Synflow walker system takes the accelerated crop flow offered by the APS system and adds an additional separator drum after the threshing drum. A 750mm-diameter threshing drum gives a shallower concave angle, designed to give flatter, gentler straw flow, cutting load on the threshing system.
He says: It is smoother and quieter to drive and also saves power. We have seen fuel consumption fall by 25 per cent from our previous combine, from 16 litres/ha to 12 litres/ha, and that is chopping all crops.
Fuel savings come despite a slightly larger engine. The 507hp Mercedes Benz power unit is also the first on the farms combines to use Ad Blue, which adds the usual level of irritation, with Mr Ascroft ensuring a convenient supply with a pick-up bed mounted tank. He also notes that the engine appears to run hotter than previous versions.
A new variable fan cooling system draws clean air in from above the combine and blows it down the sides of the machine and Mr Morris finds this much cleaner.
He says: We would normally have to blow down the combine every other day, but it will now go for two or three days. Servicing is very straightforward, with just three grease nipples to tend to on a daily basis, although I would prefer to see the bearings than pump into a remote greasing system.
Output in spring barley was about 45ha/day last season, averaging 30t/hour, but spot rates of 40t/hour have been achieved.
Mr Ascroft says: We do not get big yields on this soil. Our five-year average for wheat is 8.4t/ha, but our aim is for a lean and simple system, and with the high grain quality that we are seeing the Lexion 6900TT really meets our needs.
Automation of settings is not especially new, but it has now been refined so we can really rely on it and it makes for an easier harvest while maintaining crop quality.
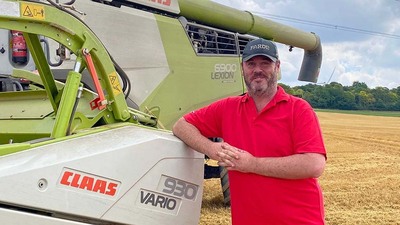
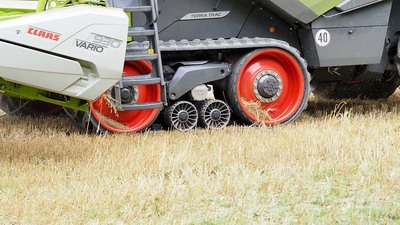
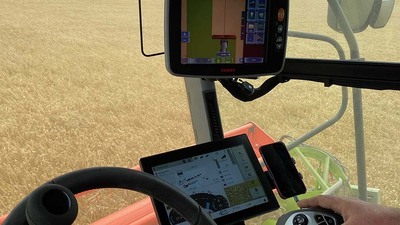
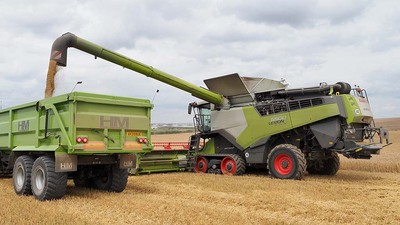