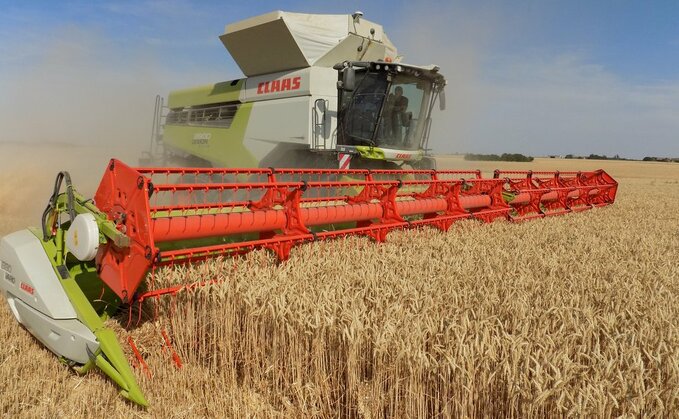
Not one to rest on its laurels, Claas has gone back to the drawing board to give its Lexion combine range a comprehensive overhaul. James Rickard reports.
In what is billed as the company's biggest investment since the launch of the original Lexion combine nearly 25 years ago, Claas recently took the wraps off its latest generation hybrid machines. Now topping out at 790hp with a new flagship model, it is a long way from the original 375hp, 480 Lexion launched in 1995.
Though its subtle styling would suggest otherwise, underneath the tinwork the combine has been comprehensively overhauled, with 65 per cent of its major components changed. These include a redesigned threshing and separating system, upgraded grain handling system, new powertrain, new engines, new transmission, new chassis and enhanced automated features.
Designated the 1000 Series, all Lexion hybrids have been replaced with an expanded seven-model line-up, comprising four narrow body 7000 series models and three wide body 8000 series machines (see range overview panel). Wide body and narrow body machines refer to the width of the threshing unit/crop channel; the narrow body is 1.4m while the wider body 1.7m.
For now, there is no change to the straw walker Lexion line-up for the UK market, though the launch event did provide a glimpse of the new 5000 and 6000 series machines yet to come.
Adam Hayward, Claas UK combine harvester specialist explains the demand for larger machines; "We have seen from sales figures that there is a clear trend towards going bigger - our most popular Lexion models have always been the three biggest."
Work began on the second generation Lexion range 10 years ago, with an almost ‘blank sheet' approach to its design. On top of 8,000 hours ‘bench' testing, the new combines underwent eight years of field testing, clocking up 6,000 hours across 10 countries. Of the 200-plus pre-production machines already out in the field, 18 of those are currently munching their way through UK crops.
Second-gen Lexions are available now, with orders being taken for next season.
Lexion hybrid range overview
Lexion model | Body width | Grain tank options (litres) | Maximum power (hp) | Engine |
8900 | 15,000/18,000 | 16.2-litre, MAN | ||
8800 | 13,500/15,000 | 15.6-Litre, Mercedes Benz | ||
8700 | 12,500/13,500 | 15.6-Litre, Mercedes Benz | ||
7700 | 12,500/13,500 | 12.4-litre, MAN | ||
7600 | 11,000/12,500 | 12.4-litre, MAN | ||
7500 | 10,000/11,000 | 10.7-litre, Mercedes Benz | ||
7400 | 10.7-litre, Mercedes Benz |
Threshing and separation
Threshing
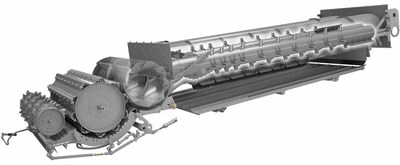
At the heart of the new combine is a heavily updated version of the firm's hybrid threshing and separation system, made up of three lateral drums, and two longitudinal rotors. Labelled APS Synflow, the new name refers to its continued use of the APS (Accelerated Pre Separation) system, along with the newly added benefit of speed synchronisation of all three drums - you adjust one and the others will automatically adjust.
Taking care of 70 per cent of separation, a major update is to the size of the threshing drum, which is now 755mm in diameter, some 26 per cent larger than the outgoing model. This greater circumference means the concave is also larger, but crucially, its reduced wrap angle means it is ‘flatter', allowing for a smoother crop flow and therefore less grain and straw damage.
In addition, 10 rasp bars are now employed on the threshing drum, which along with its greater diameter, means drum speed can be run slower; down to 550rpm compared to 750rpm. Total speed range is from 330rpm to 930rpm.
Rasp bars are also positioned at ‘gentler' angles, offering less wear and better performance, as they are operating over a larger surface area, says the manufacturer.
In comparison to the current wide body models, with a threshing area of 1.26sq.m, new wide and narrow body models have an area of 1.55sq.m and 1.3sq.m respectively.
threshing 2
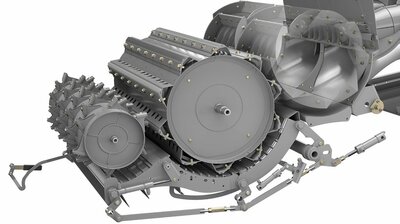
For easier adaptation to crops and conditions, up to 40 per cent of the main threshing concave can be interchanged, via access from the sides of the combine. Side panels are also considerably lighter and easier to handle. Further concaves under the accelerator can be accessed via the stone trap.
As well as concave distance adjustment, which is now parallel across the accelerator and threshing concaves, an extension to the threshing area can be achieved by pivoting into position an extra abrasive edge to the concave. Additional control to the threshing area comes from ‘flaps' which can be engaged to cover the front 10 per cent of the threshing concave, giving a more aggressive thresh in tougher conditions, or reducing the area in drier situations.
In all, there is a much greater range of control over the threshing area, much of which is tied into the combine's automated systems. Manual intervention is also eased with improved access and easier set-up, particularly concaves.
sep pic and text
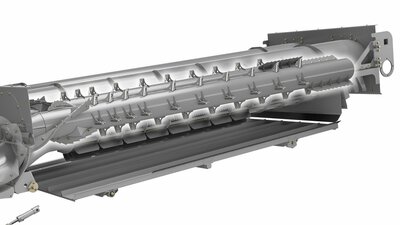
Smoothing out the transition from threshing drum to separation rotors, the new 600mm diameter feed drum has been increased in size by 57 per cent. This allows for a larger chevron segments, giving a more precise feed of material to the rotors, says Claas. In addition, rotor angle has been ‘flattened out' adding to the improved crop flow and reduce the chances of ‘sticky' crops, such as linseed and beans, from balling up.
Looking after the final 30 per cent of separation, a new rotor grate design is claimed to be gentler on the straw, while offering greater separation. To reflect the high throughput, the top two models get six rotor grates and operate a at rotor speed of 450-1,250rpm, while the rest get five grates and operate from 370-1,050rpm. Adding to this, rotor bearings and hangers have all been beefed up.
Like the threshing area, there is much more control over separation area, which sees extra rotor covers (bomb doors) added to the Lexion; four as standard on the top two models, and two as standard on the rest with the option of four. These allow the separation area to be increased or decreased based on the conditions. They also help to avoid overloading the sieves with unnecessary amounts of trash and chaff.
Grain handling
grain hand 2
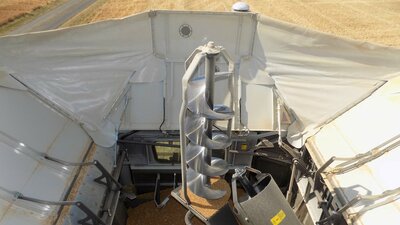
Getting close to powerline territory, the top model can be specified with a whopping 18,000 litre grain tank. If the grain is 800 grams/litre, this equates to 14.4 tonnes in the tank.
Equally as impressive, on models with 13,500 litre tanks and above, unloading is via a 420mm diameter auger offering 180l/sec. For all tank sizes, emptying is in about 100 seconds or less, says the manufacturer.
Thanks to a new gearbox design, further control of unloading grain flow can be achieved, with the ability to shut down one of the two cross augers, halving flow.
Auger length options range from seven to 11 metres, which also now has an extra 4 degrees pivot angle forwards. It may not sound like much, but it does help with visibility when unloading.
For greater accuracy, five level sensors are used in the tank, giving a much truer reading on slopes. Amazingly, for the first time, the tank now features steps for much safer access. It also gets pin-adjustable slides over the cross augers which are easier to alter.
gran tank 3
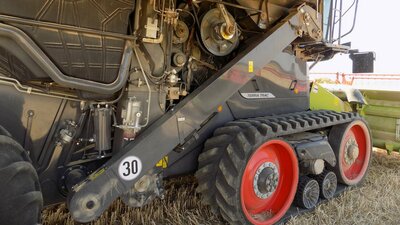
On the other side of the combine, both grain elevator and returns system capacity have been increased, by up to 47 (wide body) and 30 per cent respectively.
Improvements have also been made to yield monitoring, which is now achieved by a force-based measurement rather than volumetric. This sees a baffle plate, connected via strain gauges, positioned at the top of the main grain elevator, which allows for yield readings accurate to within 1.5-3 per cent, says the manufacturer. It is also less susceptible to inclination of the machine and elevator tension. And it only needs calibrating once per crop per year.
Driveline and engine
driveline
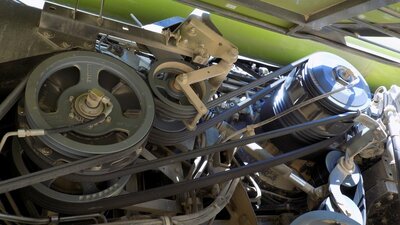
Taking inspiration from the firm's Jaguar foragers, the driveline has been completely reconfigured, putting all major drives down the left hand side of the combine. This means no more routing through diesel tanks, which now reside neatly on the right hand side.
A new drive engagement system has also been developed. Rather than simply relying on belts which are hydraulically tensioned around a pulley, drive is now engaged via a clutch. Hydraulic tension, though, is still employed, which releases all belt tension when the combine is keyed off, and vice versa. In all, this has the upshot of better belt protection, and you don't get that sound similar to a Jack Russel being stepped on.
Interestingly, the Jag's driveline is rated to about 1,000hp, pointing towards the futureproofing of this combine.
Also taken from the foragers is the firm's Dynamic Power system, whereby if the combine senses it does not need all of the engine's power, it will automatically switch to a lower-powered map. This is done in increments of 20hp, in 10 steps and is said to save fuel. Similarly, rated engine speeds have been reduced to 1,800rpm.
Track shot
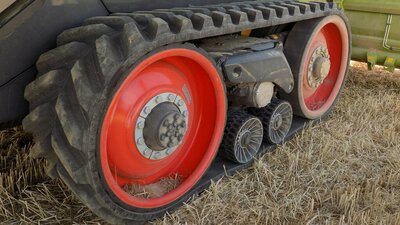
As for top speeds, all TerraTrac models can achieve 40kph, and all narrow bodied wheeled machines can reach 40kph - only the wide body models on wheels are limited to 30kph.
A new two-speed gearbox means changing range is less arduous, and its auto-park brake adds to the convenience. First gear is now faster too, up to 20kph, but you can still harvest is second gear.
For the first time, wheeled machines are available with a diff-lock, which can be controlled manually or automatically.
Underneath, the transmission has been repositioned to afford more space around it, helping airflow to the sieves. Airflow around the engine bay has also been improved, with sealed walkways helping direct air and prevent dust settling in unwanted areas. Side ventilation is also greater.
Biggest front tyre sizes are up to 2.15m, rears up to 1.75m, while track widths range from the popular 635mm to the 890mm units. All Lexions now get a four-link rear axle, allowing the required movement to accommodate larger tyres, but prevent fouling when travelling over uneven ground.
Cab, controls and technology
wide cab shot
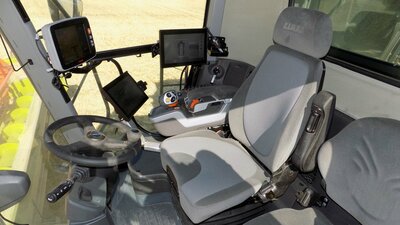
As for cab frame, things are fairly status quo. A slight difference is an extra 15cm of space at the rear of the cab, allowing for more shoulder room and a larger grain tank window. Sound insulation has also been improved and it gets a more powerful fridge.
The most noticeable difference is the adoption of a completely new control concept, as shown for the first time last year on its Tucano combines. As well as a more ergonomic layout of controls and a new Cebis touch screen terminal, it offers users more flexibility when it comes to set-up. As such it will keep various generations of operators happy, with the ability set the machine up via physical buttons, a navigation dial or directly through the screen.
The screen, too, is a quantum leap away from its predecessor and affords, in typical Claas style, clear and clinical navigation and set-up, along with increased functionality.
cebis
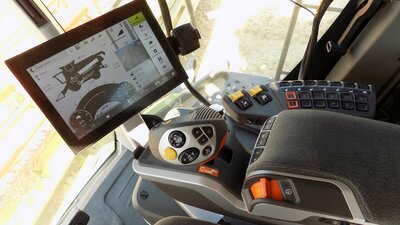
Building on its suite of automated combine offerings, the firm's Cemos Automatic system, first introduced in 2017, has been further developed. Featuring more sensor inputs and greater adjustment, the system constantly monitors all machine parameters, ultimately to keep grain quality and performance up and fuel use down.
This is achieved by selecting a combining strategy via priority sliders on screen. Emphasis can be put on grain quality, straw quality, sample cleanliness and throughput, for example.
From an operation point of view, it is a big driver aid, and one which will flatter. However, it is not a replacement for a good operator, more of an assistance to get the most out of this high capacity machine.
cemos
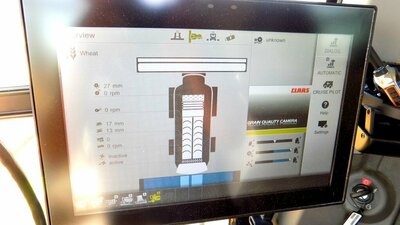
According to Claas, it is a growing option, and even the best operators will only beat the system for two hours, before distractions and fatigue takes over. However, to get the best out of it, it does need to be used all day so it can ‘learn', not just turn it on when you get tired.
Cemos Automatic can be run through the combine's main Cebis terminal, or for better visualisation of what it is doing, a second screen cab be specified. At present, it will work with wheat, barley, rape, beans and maize. Oats are being worked on.
Though the main screen can be swung out of the way, once you add a second screen for Cemos Automatic, and one for guidance, the right hand side of the cab does start to get cluttered, which eats into sightlines - not something you want when you are trying to keep an eye on a 13.8m header.
field scanner
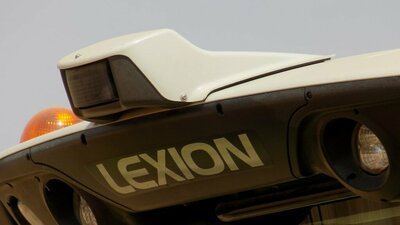
Replacing its laser pilot guidance system with radar-based technology borrowed from Audi, Claas has come up with a version which is less susceptible to dust and easier to use.
Now mounted in the centre of the cab roof (previously at the ends of the header), it has the ability to follow the left and right hand edges of crops, but can now also follow tramlines. Its new position also means it does not need calibrating between crops.
Feeder housing and headers
convio

Up front, Claas has added to its range of Convio draper headers it previewed last year. Five models range from 7.69 to 13.79m, with fixed and flexible versions available.
In addition, new Vario header features include more sensing bands for better contour following, more lights, optional stabiliser wheels for wider headers, and quick release fingers.
Geared up for larger headers, elevators have been beefed up and larger lift cylinders employed. In turn, the feeder house is deeper to cope with more material.
Three feeder house face plate options are available; fixed position, manual pitch adjustment via bolts, and hydraulic pitch adjustment. Automatic lateral adjustment is standard on all.
feeder house
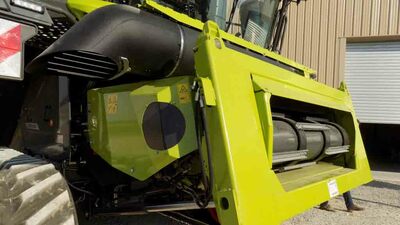
Keeping it clean, feeder house dust extraction has been boosted, and a new external fan is positioned to keep the top of the elevator free from dust and awns. Both systems blow debris down the right hand side of the combine, away from the cab and steps - very noticeable by the build-up of dust on the rim of the wheeled machines.
Preventing stone damage, a new self-cleaning stone trap means you do not need to go crawling under the combine to get all the stones out, with stones ejected via a bar. The ‘pegged' design of the accelerator drum also helps against stone protection.
New-gen Lexion line-up; 5000, 6000, 7000 and 8000
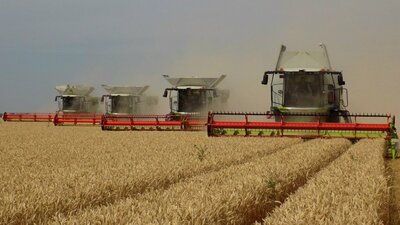
Verdict
All Lexion hybrid - threshing drum plus rotary separation - combines have been replaced with an expanded seven-model line-up, comprising four narrow body 7000 series models and three wide body 8000 series machines topping out at 790hp with a new flagship model.
New threshing system components, revised separation rotors and a revamped cleaning system all contribute to increased output.