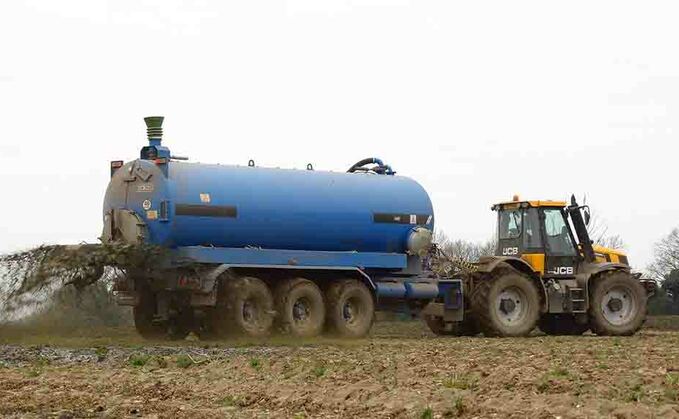
Contractors and farmers are always looking for ways to maximise the output of their machinery, given the substantial cost it takes to buy.
Alex Heath speaks to an early adopter of a system which uses a trailer chassis onto which trailer bodies and tanks can be added.
Conventional trailers often sit redundant for large periods of the year.
However, for one East Anglian contractor, a Stewart trailer chassis is providingthe ideal platform for a multi-purpose role in the contracting fleet.
Steve Suggitt, owner of Suggitt Farm Service, Attleborough, Norfolk, has been running Stewart chassis of varying axle configurations since 2009.
He says the principal is simple and works well for his varied and constant workload. Bought as conventional trailers, the latest editions are based on the Stewart tri-axle RoadKings with 20-tonne bodies.
Hi-Spec tanks are then added to the chassis using the same fixing mechanism as the trailer bodies.
Mr Suggitt says the idea and design was done by himself and his team, with a number of different tank sizes tried throughout the years.
He says: "Trailers would be sat unused for most of the year, except for silage and maize harvest. We had increasing demand for slurry work, mainly from anaerobic digester units which have been going up at a rapid pace around here, and the cost of buying tankers to carry out this work was considerable."
Application
He says the demount chassis are used more for tanker work than they are for trailer work. The tankers are typically used for road transport to service his Joskin Euroliner 28cu.m tanker with 24m dribble bar, but can be used for application via a splash plate at busy times.
Top emptying suction cups are fitted to facilitate quick unloading times.
"The most important factors these days for me are cost of ownership, build quality and safety, of which the Stewart chassis and Hi-Spec tank combination ticks all these boxes."
He says the trailers are bought from Alan Suffling of SAS Agri. Mr Suggit says the Stewart trailers have the best build quality of any make available, with his first demounts being changed earlier this year after 10 years of hard graft, with no structural issues.
On the safety front, the tanks are attached the same as the tipping trailers, using a large pin at the rear and the hydraulic tipping rams holding the tank in place. This has the added benefit of allowing the tank to be tipped up, handy when working on sand-bedded dairy farms where the bottom of the tank gets sand settling in.
"We can tip the tank up and give it a quick wash out, meaning no-one has to go in, which is potentially very dangerous."
Baffles inside the tanks allow them to be partially filled to run at the legal weight on the road, but if doing fieldwork, they can be filled to their maximum, which is 20cu.m for the smaller of the pair and 21.3cu.m for the larger one.
Several options have been considered over the years, including single-axle vacuum tanks and purpose- built ferrying tanks. However, he says the flexibility these chassis with interchangeable bodies offer is one of the reasons this route has been taken.
The other determining factor is cost, being able to use the chassis nearly every day of the year for varying tasks, rather than having trailers and tanks sat redundant for extended periods.
He says spreading the cost of the running gear across 52 weeks, rather than the busy periods for conventional single use, enables him to pass the savings of capital outlay onto his customers.
Having used this system for 10 years, Mr Suggitt is convinced this is an economic way of operating a contracting fleet, using the expensive components; the chassis and running gear to its full potential.
"Safety and efficiency are priorities for any contractor. With this setup we are maximising both," Mr Suggitt says.
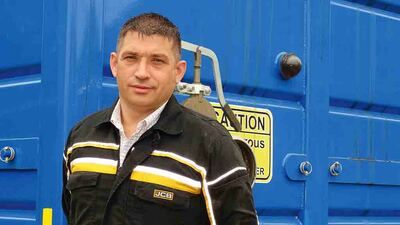
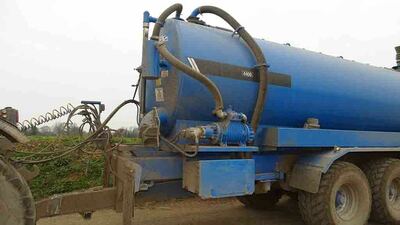
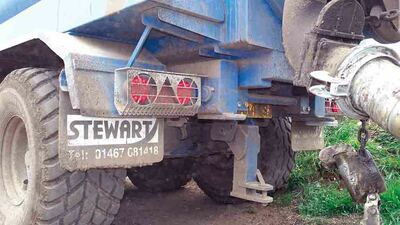
Verdict
Being able to mount a slurry tank on to a tipping trailer chassis makes year-round use of a single set of costly running gear.