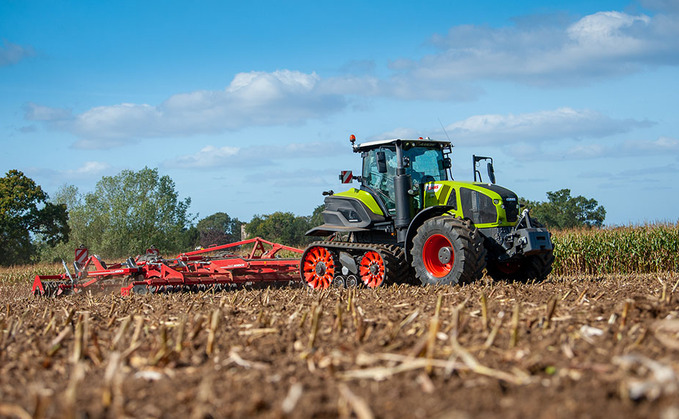
Launching at Agritechnica, Claas has made several updates to its tractor offerings, including a half-track development for its Axion range, greater torque for its equal-wheeled Xerion tractors and more functionality for its Arion models. Alex Heath reports.
Having been out of the tracked tractor game for nearly 20 years, Claas has made a return to the crawler market with its half-tracked Axion 900 range.
However, that is not to say the manufacturer has been absent from track developments for all those years - its Lexion combine range in particular has been making use of the firm's Terra Trac system for over 30 years.
When production of the 410hp Claas 95 Challenger stopped in the early noughties, market demand at the time was not sufficient enough at the time for such a style of tractor.
However, the company now sees an opening for its latest incarnation of tracked prime movers, and believes a half track design provides a good mix of traction and manoeuvrability while maintaining versatility.
With tightening farm profits and increasing overheads machinery costs are coming under growing scrutiny, says the company's UK tractor brand manager, Steffan Kurtz.
He says that where farms typically relied on a twin track machine to do 400 to 500 hours of work per year, typically cultivating and drilling, now there has been a shift in demand toward high horsepower multi-trick work horses.
This includes tasks such as grain chasing, baling, frequent shallow cultivations, top dressing and spraying, with the aim now of increasing machine workload to 1,200 hours or more each year.
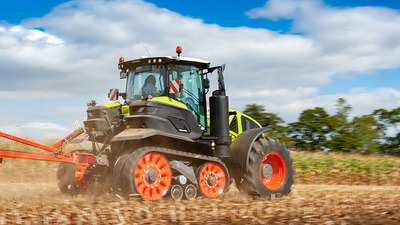
text
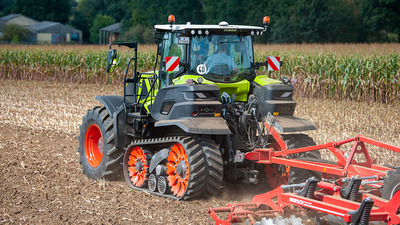
This has led the German giant to develop a tractor that can perform any tasks its wheeled equivalent can perform, but with boosted performance in some scenarios, such as draft work. Following 35,000 hours of infield and road testing in Romania and France, plus four pre-production models working in the UK, the Terra Trac variants will enter full production in 2020.
Initially the company is offering two Terra Trac models, based on the 355hp Axion 930 and 445hp Axion 960 frames. Power still comes from the 8.7-litre Cursor 9 engine from FPT. But, it is not simply a case of bolting a set of tracks onto the chassis.
As the tracks will be under more pulling load rather than carrying load, as they would be on a combine, the tracks themselves have been redeveloped to utilise the torque available to them. As such, they feature a larger drive wheel at the rear, creating an elongated egg shaped profile. And while the tracks available in 635, 735 and 890mm widths might be the same as those used under the combines, the rest of the running gear has been changed.
This includes the use of spoked wheels with rubber pads, which aids cleaning, a problem identified with the Lexion versions. Lugs on the inside of the track keep it straight on the assembly, with drive coming through friction, ensured by an hydraulic tensioning system.
text
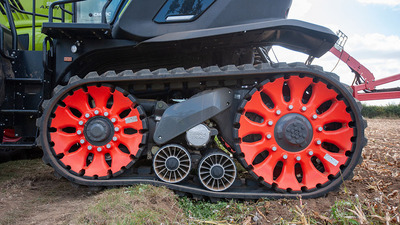
For comfort, the Axion TT uses three methods of suspension, including front axle and four point cab, as well as a hydraulic displacement system within the track unit. The company says this makes the tractor more comfortable than its wheeled version. While we might not go that far, as you can still feel a murmur of shuffling along on tracks, it is by no means uncomfortable, even at its top speed of 45kph whisking down headlands.
The other reason for giving the tracks suspension, is to allow for a constant footprint which is always in contact with the ground. When compared to a 900mm tyre on 42 inch rims, the 890mm-wide track has a footprint 35 per cent larger, at 3.87sq.m. As a result, the company says the tractor kinder to the ground, while also producing 15 per cent more tractive power.
The suspension system allows the track to oscillate when traversing over bumps; eight degrees downwards and 15 upwards. By doing this, it keeps the track in contact all of the time, and stops incidences seen with twin track and other half track machines where the front axle is overloaded, or pointed skyward, before coming back down to the ground with an uncomfortable thud.
pic
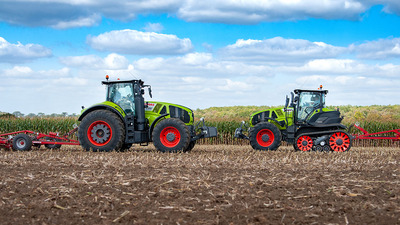
text
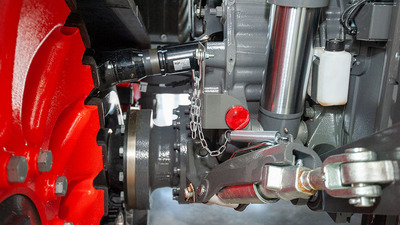
To get the tracks attached, the trumpet housings normally found coming out of the rear differential are gone, as is the diff, with ‘saxophone' style housing dropping the attachment point down to the tracks. Drive comes directly from the planetary gears in the rear-end via cardan shafts, at high speed/low torque, before the low speed/high torque reduction happens in the track unit. The geometry of the rear-end has also been adapted, and now sits 200mm further back, but can still lift in excess of 10 tonnes.
Weight distribution is 67:33 in favour of the rear, before a weight block is added to the front end, evening it up. Unladen, the tractor sits at 16.5 tonnes, about 1,500kg heavier than the wheeled model. It can be ballasted up to 22t.
To make room for the tracks and utilise the free space above them, the fuel and AdBlue tanks have been moved to form the rear fenders, with tank capacities of 860 and 90 litres respectively.
text
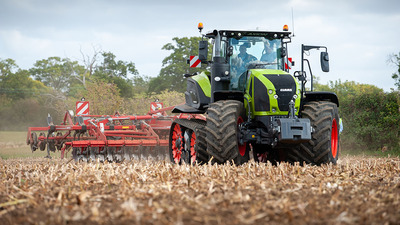
A major concern for many prospective buyers would be scuffing and smearing when turning on the headlands, as well as damage to the track units. However, the manufacturer has found a solution to this issue.
At speeds below 12kph, when the steering wheel is turned, the inside brake is activated, slowing the rate at which the track is spinning. This allows the machine to turn with similar agility to the wheeled version. The amount of braking required can be chosen through the Cebis screen. Sensors measure the temperature of the brakes, with fail safe protection of the units once the temperature rises above 140 degrees Celsius.
With the introduction of the track units, the tractor can now be lifted or lowered for the best ride height for a specific job. For instance, the low position could be used when cultivating, while the raised position could be used for baling or grain carting to prevent swaths from being pulled along.
Gearbox-wise, the new tractor is only available with the company's CMatic continuously variable transmission.
pic
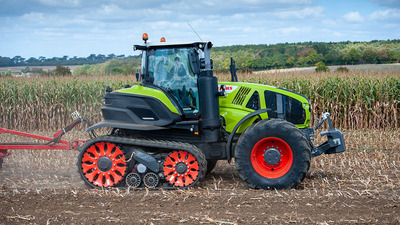