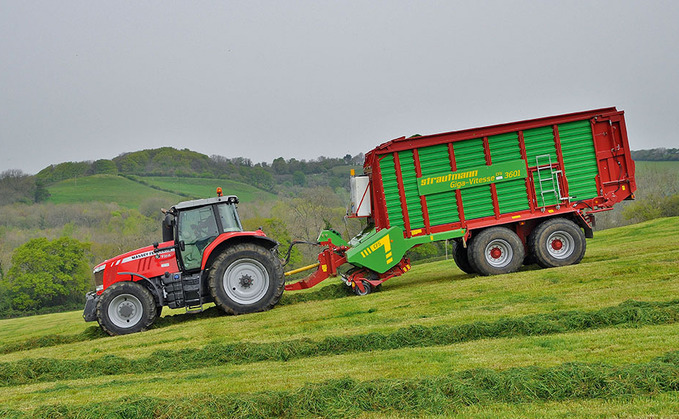
Dorset contractor Craig Frampton harvests 2,200 hectares of grass each year using two Strautmann Giga-Vitesse CFS 3601 forage wagons.
In the West Country, where steep rolling hills and winding valleys form picture postcard views, gathering grass for silage can present a range of interesting challenges.
While lowland farmers predominantly favour the selfpropelled forage harvester, those faced with harvesting grass on bank fields with unforgiving inclines are increasingly favouring the forage wagon, as Dorset contractor Craig Frampton reveals.
"A forage wagon combines the harvesting and transportation aspects of silage-making into a oneman operation.
"As a result, it gives the farmer the flexibility to manage his harvesting schedule around factors such as his daily livestock duties and the weather, as it is suited for harvesting smaller, more manageable acreages.
"My father started our contracting business back in 1994," says Mr Frampton.
"We started out baling grass for silage and it developed from there, but we have never owned a trailed, or a self-propelled forage harvester.
"About 10 years ago, I started getting enquiries from farmers who wanted to know if we had a forage wagon.
"In 2010, we took the plunge and purchased our first Strautmann, which did just 200 hectares the first season. The following year it did 600ha and the business has grown from there."
Today, P. and L. Frampton and Sons harvests about 2,200ha of grass using two Strautmann Giga Vitesse CFS 3601 forage wagons, which in terms of capacity have a compressed loading volume of 64.6cu.m, which equates to between 10-12 tonnes of grass, depending on the crop.
Comparison
To make a comparison in terms of weight, a Claas Jaguar 870 SPFH equipped with a Claas 300 pick-up weighs about 14t dressed for battle.
The forage wagon tips the scales at 9t unladen which, when added to the weight of Mr Frampton's MF 7724 tractor, gives a combined weight of about 18t.
"When the wagon is full, the gross vehicle weight is about 30t," says Mr Frampton.
"It is not vehicle weight which is the problem for contractors around here. A modern self-propelled harvester with a driven steering axle would cope with the banks, however it is the fleet of tractors and trailers required to keep it going which create the problems.
"Many of the farms we work on can only be reached by narrow roads and tracks, often with over-hanging trees. The gateways are also very narrow and they can sometimes be really awkward to access.
"Not only are they difficult for a large self-propelled machine, the constant flow of trailer traffic compounds the risk of damaging verges, gate posts, fences and walls, in addition to increasing the risk of damaging your own equipment.
"One of the biggest problems we have in this part of the country is finding good operators. Finding drivers who have experience working on hills and banks is increasingly difficult, and this is another reason why the forage wagon stands out as the most effective tool for harvesting grass."
The silage teams employed by Mr Frampton include one man on the mower, one man on the rake and another on the silage clamp.
Driving one of the forage wagons himself, Mr Frampton reveals each machine can harvest an average of 24ha per day, increasing to 40ha in larger fields and lighter crops.
The Strautmann Giga-Vitesse CFS 3601 has a power requirement of just 145hp. Yet working on steep inclines requires considerably more power if the tractor is to maintain control of a loaded wagon, says Mr Frampton.
"Our Valtra T174 tractors will comfortably power a wagon of this size, but they do not have the grunt to keep moving on the bank fields. You need a heavier tractor with more power and I find MF 7724 Dyna-VT is about the perfect size.
"It has got the weight and power you need, it is manoeuvrable enough to fit through narrow gateways, and the CVT gearbox gives me precise speed control. Personally, I think it is the perfect tractor for this particular job."
Mr Frampton disagrees: "Why would you use a £90,000 Strautmann for carting maize?
"You are just adding unnecessary wear to your forage wagon, for one-third of its potential hourly working rate," he says.
Where zero-grazing is concerned, Mr Frampton can see the benefits for intensive dairy farmers, but only if they personally own a forage wagon.
"I know a farmer who uses a wagon for zero-grazing. It takes him about an hour each morning to cut the crop and tip it.
"He uses a front-mounted mower which he leaves in the field after he has finished loading, because you cannot get the tractor and wagon through his gateways or the farmyard with the mower attached.
"For a contractor like myself, working for a neighbour would be fine, but if I had to travel to several farms to zero-graze their cattle I would spend most of the day driving about for a couple of hours' pay.
From my perspective, it is simply not cost-effective.
"The versatility of using a forage wagon-based harvesting system has transformed our business," concludes Mr Frampton.
"We still operate three balers, but increasingly it is the quality of fodder produced by the forage wagons which our customers want."
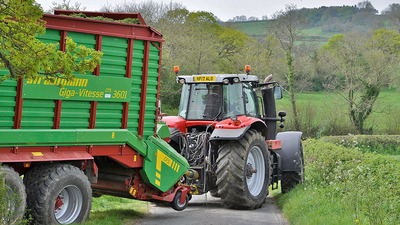
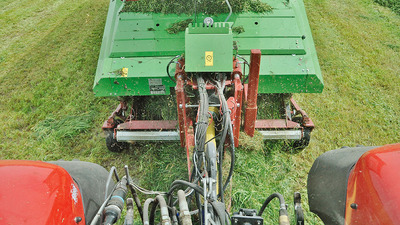
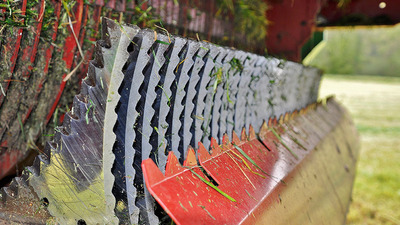