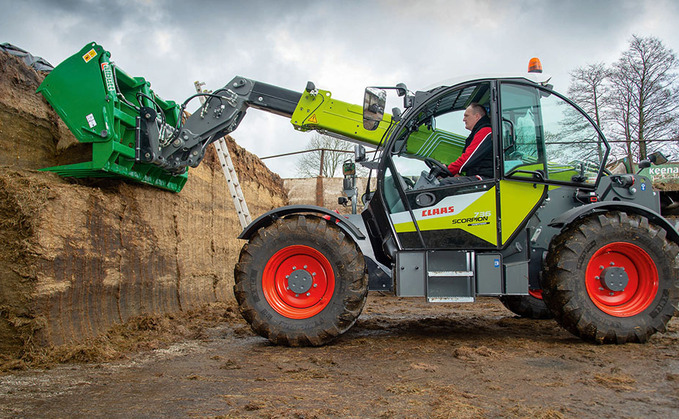
Now in partnership with Liebherr to build its telehandlers and wheeled loaders, has Claas made the right decision in teaming up with the fellow German firm?
James Rickard puts the latest Scorpion handler to the test...
Known for its quality construction machines, it would appear, on the surface at least, that Claas has made a good decision in partnering with Liebherr to build loaders.
On first impressions of its latest mid-range Scorpion telehandler, the signs are looking good.
A beefy build and a decent finish all point toward Liebherr's renowned heritage, but how far has Claas gone to make the handler its own?
The decision to develop loaders with Liebherr followed Class' ambitions to offer a greater lineup of loaders, particularly wheeled loaders which could match the capacity of its high-powered self-propelled foragers.
Video coming soon
In addition, Liebherr was also drawn to Claas to get its products into an ag market. However, this meant a parting of ways from long-time partner Kramer, which now has a strategic alliance with John Deere.
As a result, Claas today has a whole new line-up of telehandlers, with seven models offering lift capacities from 3.2-5.6 tonnes and lift heights from about six to 10 metres.
Having been suitably impressed by the Kramer built-machines during a test drive back in 2014, how do the new Scorpions fare?
Test machine specifications
? Model: Claas 736 Scorpion Varipower
? Lift capacity: 3,600kg
? Lift height: 6,930mm
? Hydraulic pump capacity: 160 litres/min (200 litres/min optional)
? Engine: 3.6-litre, four-cylinder, Deutz
? Power: 136hp
? Transmission: Hydrostatic
? Wheelbase: 2,850mm
? Overall width (excluding mirrors): 2,380mm
? Overall height (depending on tyres): 2,465mm
? Base retail price: £108,560 (same price as model tested)
CAB
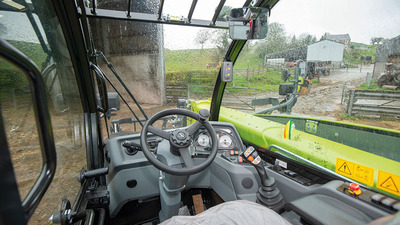
ONE of the key areas Claas was keen to develop with the latest Scorpions was the visibility, particularly the area to the right rear quarter.
For a telehandler of this size, the firm has done a good job. The bonnet neatly slopes away from you, while exhaust and main boom pivot point are kept low.
It adds up to good views all-round, with the ability to see all four tyres, or at least the tops of them, which is something many telehandlers struggle with. It also means less reliance on mirrors, which is a good thing when working in confined spaces.
Cab space is decent, even for tall operators, though be aware of the rear view mirror when climbing in. But rather than coming out of the front of the cab, the steering column comes up out of the floor in a harvester style. While it does offer plenty of adjustment, it does impede access and exit slightly.
Access is good overall, however, the door does not close flush with the cab frame, and when the top half is folded back, it sticks out a good 6in. Claas says it has now recitified this.
Also, when the top half is either partially or fully opened, latches rattle, so could do with being snugger.
In-cab storage extends to a sturdy metal storage compartment under the seat, with just enough space for a couple of straps and chains.
CONTROLS
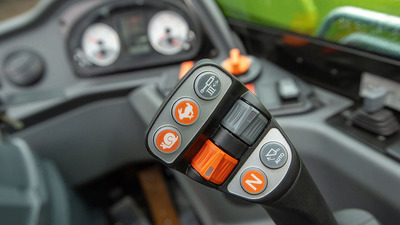
GREETING you in the 736 is an almost minimalist operator environment.
Most dials and switchgear are biased towards the right of the cab, however, there are a few switches hiding in the cab's roof lining, which can take some finding for new operators, including the diverter valve switch for the headstock locking mechanism.
Switches
Once you have found the switches, clear icons mean most buttons are easy to fathom.
The joystick does not move with the seat; this is reserved for 746 and 756 models. However, it is in a relatively convenient position and you do not have to press an awkward ‘consent' switch to make it work.
Joystick buttons and switches are well laid out, and by having boom extend/retract and shuttle controls on the face of the ‘stick and the third service on the rear, it means you can carry out multiple operations at once. Joystick actions are smooth and responsive and all controls are proportional.
For fans of a left-hand shuttle lever, unfortunately this can only be done via a switch on the joystick.
HYDRAULICS
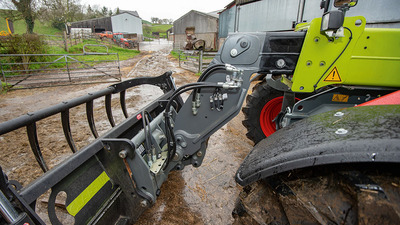
HYDRAULIC flow rate on the 736 is seriously impressive, with 160 litres/minute on tap from a load sensing pump.
It makes light work of multiple actions, cutting down on those important cycle times. If that is not enough, you can up-spec the machine with a 200 litres/min unit.
There are no silly handling modes to select like some manufacturers have to work around the safe load limit legislation, it is just jump on and drive.
However, we do miss a couple of useful features from the old Scorpion, such as bucket and pallet modes, which automated boom extend/retract depending on application.
As a consolation there is Smart Loading, an optional return to dig feature which can be ‘unlocked' via the machine's software.
As standard, you can lock out the tilt and crowd movement, useful for when using a man basket.
For convenience, the machine features both internal and external auxiliary ‘dump' switches. These are really handy for taking pressure out of the third service, making hooking up attachments easier.
Couplings are conveniently located on the headstock, meaning hoses are kept to a minimum, and there is the option of a fourth service.
Comfort-wise, boom suspension can be operated in one of three modes; off, automatic (cuts off above 15kph), and on full-time.
However, while vertical shock loads are taken care of, it could also do with some extra end-boom dampening. As it is, when the boom is fully extended or retracted, you are greeted with a sudden bang when it reaches its limit.
HANDLING
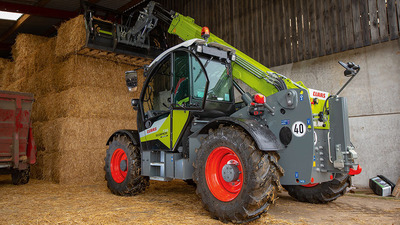
SPORTING an element of oneupmanship, the Scorpion features not the usual three steering modes, but four: front-wheel, four-wheel, crab and adjustable crab.
The latter is a blend of front-wheel steer and crab-steer, and allows the rear steering angle to be set in any position, leaving steering to be done by the front wheels, which is ideal if you want to run down a feed passage at an angle, but retain greater control over steering, compared to just using full crab mode.
When switching between steering modes, all steering alignment is automatic.
Helping stability, the new Liebherr-built models are about 10cm wider than previous machines, and the boom is in a more central position, reducing twisting forces.
But unlike Kramer-built machines, which featured lateral boom supports, holding the boom in place when pushing into a heap, for example, the Liebherr machine, as do most makes, relies only on the rear pins and bushes.
However, its construction-spec background brings with it plenty of metal and sees double-walled plates to support the main pin and bush.
Tearout force is also boosted over old Scorpions, thanks to revised geometry of the headstock linkage. This also affords plenty of tilt and crowd.
Auto-greasing is an option, although without it, grease points are still usefully grouped together.
ENGINE AND TRANSMISSION
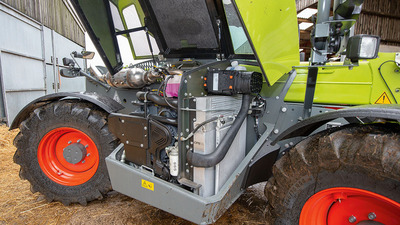
AS it was originally a Claasinfluenced design, the new models stick with a similar powertrain concept with power coming from Deutz and a GKN Watterscheid-built hydrostatic transmission. But unlike the Kramer machine, the engine sits sideways in the engine bay, improving access, says Claas.
Airflow sees air drawn in at the front of the bay and expelled out the rear, with radiators positioned towards the front of the bay.
On-demand cooling sees the radiator fan only work as much as it needs to, which can also be reversed either automatically or manually. In auto-mode, the intervals are every 30 minutes.
To meet Stage 4 emission compliance, it uses a combination of selective catalytic reduction and a diesel oxidation catalyst, so no diesel particulate filter to worry about.
In keeping with its bullet-proof build, all tanks on the machine are metal, and underneath a belly plate, which looks like it could withstand an anti-tank mine, runs the full width of the machine.
As with all Scorpion models, power is transmitted to the wheels via a single range, wide-angle hydrostatic transmission, offering seamless speed adjustment from 0-40kph.
Within this, the transmission can be operated in one of three ‘virtual' ranges: 0-15kph, 0-30kph and 0-40kph. These can also be toggled through on the go.
In each range, you get 100 per cent pedal travel, which is proportional to the speed range selected. For example, this really helps when carrying out precise movements in low range.
The brake pedal also doubles up as an inching pedal, allowing the feathering of hydraulics and no need for a third pedal, which is a very neat solution.
DRIVING CHARACTERISTICS
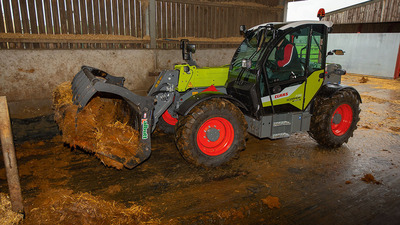
AS with most hydrostatic machines, when you come off the throttle, the transmission provides a good amount of braking, without having to resort to using the actual brakes.
Also, when stationary, the transmission will ‘hold' the handler on a hill.
Overall, the transmission offers good adaptability to jobs, while keeping things smooth and simple.
It is also responsive, requiring little encouragement from the throttle pedal to get going.
If further functionality is desired, you can spec the machine with independent throttle and forward speed controls, facilitated by two ‘paddles', which are useful for dispensing buckets, for example, where you need a constant engine speed and variable forward speed.
In addition, its Smart Roading feature, like a tractor's continuously variable transmission, reduces engine revs on the road, but maintains top speed, reducing noise, fuel use and wear and tear.
It also has an automatic handbrake which kicks in when neutral is selected, if you leave the seat, or if the machine has been stationary for longer than five seconds. As soon as the throttle is touched, it deactivates.
Finally, to aid traction, the machine features a 45 per cent locking, limited slip differential on the front axle, so no manual engagement is required.
VERDICT
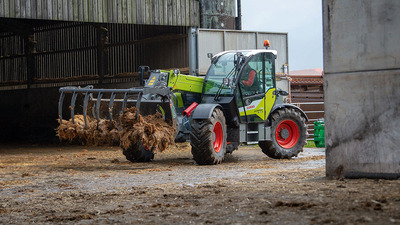
IT is fair to say we were not sure what to expect with the Liebherr-built machine. While the manufacturer is well-known for its quality machines in the construction industry, telehandlers are not perceived in the same way as they are in the agricultural industry.
As such, machines are generally specced and bought to a price, and therefore do not come with all the creature comforts we value in farming.
Thankfully, Claas' influence on its development addressed this, bringing with it refinement and logical control.
Overall, it seems anything the Scorpion has lost with the old Kramer partnership it has made up in other ways with the collaboration with Liebherr.
Expansion
And while it might be hard to convince users to stick with the Claas brand, rather than follow what was undeniably a good product with the Kramer machines, at least with Liebherr, the firm now has a solid foundation on which to develop and expand its loader line-up.
Verdict
It is fair to say we were not sure what to expect with the Liebherr-built machine. While the manufacturer is well-known for its quality machines in the construction industry, telehandlers are not perceived in the same way as they are in the agricultural industry.
As such, machines are generally specced and bought to a price, and therefore do not come with all the creature comforts we value in farming.
Thankfully, Claas' influence on its development addressed this, bringing with it refinement and logical control.
Overall, it seems anything the Scorpion has lost with the old Kramer partnership it has made up in other ways with the collaboration with Liebherr.
And while it might be hard to convince users to stick with the Claas brand, rather than follow what was undeniably a good product with the Kramer machines, at least with Liebherr, the firm now has a solid foundation on which to develop and expand its loader line-up.