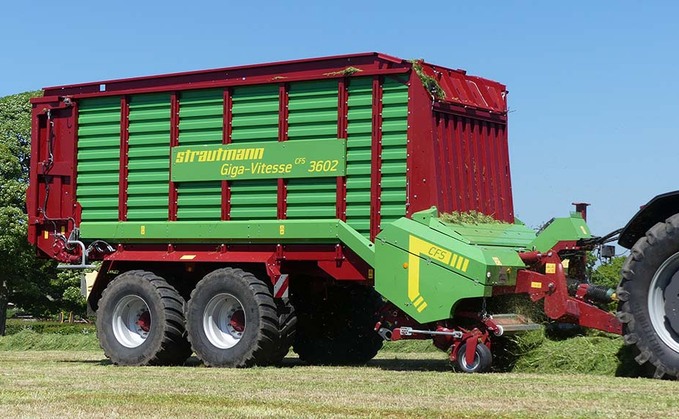
Extending its forage wagon line-up, Strautmann, distributed in the UK by Opico, has added a new 02 Series version of its popular Giga Vitesse forage wagon. To find out more, Farmers Guardian put the new machine to work.
Introduced for the 2021 season, Strautmann's latest 02 Series Giga Vitesse forage wagon builds on the success of the 01 Series and offers several new features, not least the use of innovative plastic pickup tines and clever automated systems.
Effectively, compared to the 01 machines, everything in front of the ‘box' is new on the 02, all with the ultimate aim of providing more throughput. This said, due to its narrower ‘front-end', the 01 is still very much a popular choice for those who need to negotiate tight gateways and narrow lanes.
In terms of wagon offering, the new 02 models will run alongside the current 01 machines, giving a total of seven models in the Giga Vitesse family: 01 Series ranges from 30 to 42cu.m (actual volume) capacities and 02 Series from 34 to 42cu.m.
To find out more about the new 02 Series wagon, we tried out the firm's most popular capacity machine, a 34cu.m 3602 model, in a decent crop of first cut grass. Power came courtesy of Massey Ferguson's new 8S.265 tractor, as reported on in FG, July 2.
Drawbar and driveline
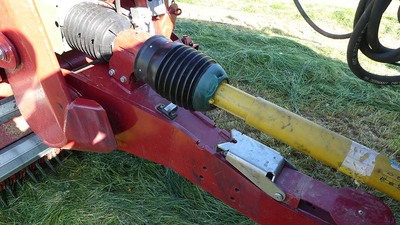
Starting at the front of the machine, the new 02 machine gets a narrower drawbar compared to the 01. This has been designed to accommodate larger tractors and their tyres, enabling a tighter turn. And with a near 300hp tractor swinging of the front of our test machine, we can confirm that there is plenty of space around the drawbar, helping a lot with manoeuvrability in tight corners and around the yard.
In addition, the first portion of the pto has also been shortened, now supported by a bearing. This keeps the pto more within the confines of the drawbar's width, reducing the chances of damage during tight turns.
Apart from one small chain to the pickup, all drive on the wagon is shaft and gearbox. From the pto, via a protective cam-clutch, this sees power take a 90-degree turn from front of the machine and sent to the right hand side. From here, a gearbox drives the feed rotor and Continuous Flow System (CFS) roller. Should the gearbox fail, it can usefully be removed without having to split the chassis.
From the left-hand end of the CFS roller, a short chain takes power to the pickup reel. And that is it. It is a reassuringly simple, robust driveline, said to be able to handle plenty of power. A shaft can also be sent to the rear from the main gearbox, if the beater option is ticked.
Pickup reel
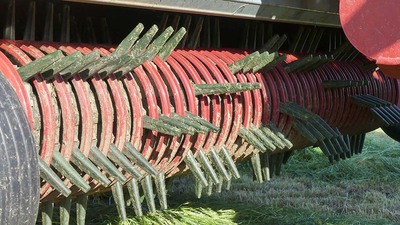
At the business end of the machine is a 2.25-metre, cam-less pickup reel featuring a double crop press roller.
But this is where convention ends, as our test model came with Strautmann's Flexload pickup option featuring plastic tines, available on 02 models. It looks a bit radical, but it makes a huge amount of sense.
Rather than a conventional steel tine arrangement, Flexload's plastic tines are mounted on a barrel inside the pickup reel, with steel bands in between the tines. Tines are arranged in a series of staggered banks, designed to provide an even crop flow into the machine, while being better able to cope with lighter, multi-cuts of grass.
The firm experimented with a helix tine arrangement which spiralled outwards from the centre of the pickup, but lighter crops had a tendency to ‘roll' outwards and not stay on the tines. This new, stepped arrangement of multiple mini-banks solves this issue, and it showed.
The plastic tines are also less prone to picking up stones; while tines are rigid from front to back, to handle heavy crops of grass, they can flex sideways, which helps them avoid picking up stones.
Maintenance has also been thought about; the tines can simply be bolted/unbolted with the steel bands in-place. As for longevity, Strautmann reports that it has not had to change any of these new type tines as of yet on its machines.
In operation, the biggest thing you notice is the near silent running of the pickup. You have to actually look to see if the machine is running. In addition, the plastic tines provided a very clean pickup, even early in the morning with a heavy dew. The pickup's decent width also helps a lot in corners, though you can still get stray lumps of grass caught under the jockey wheels, if you are not paying attention.
Jockey wheels are pin-adjustable, to help match the pickup to the conditions. Also helping the pickup to follow ground contours is its ability to pivot from side to side, as well as up and down. An optional ground following roller can also be specified, which is positioned under/behind the pickup.
As well as the Flexload plastic tine option, more conventional steel tines can also be specified, which come with plastic bands. Effectively, with either option, metal never comes in contact with metal, reducing wear.
Crop flow
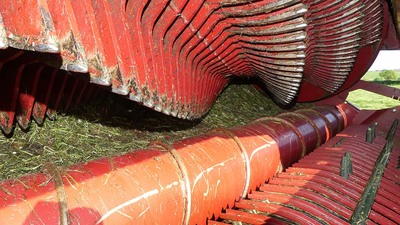
Continuing the crop flow, behind the pickup is Strautmann's famous CFS roller. Providing two jobs, CFS keeps crop flowing from the pickup to the feed rotor and does not rely on the need to ‘force' crop through to keep it going. It also features an outwardly spiralling pattern which distributes crop across the full width of the machine, providing a more even feed into the rotor and through the knife bank. In doing so, the wagon's box fills up more evenly, making the most of load space, and it is said to have a noticeable effect on knife wear, with a more even wearing of knives across the width of the knife bank.
Until you see CFS working, you cannot actually believe the difference it makes, especially in lighter crops where it is crucial to get an even feed across the width of the wagon. This said, a good rake person always helps.
Compared to the 01 which features a 1.64m feed rotor, the 02 brings with it a wider 2.1m rotor with integrated flighting at either end to bring the crop inwards. And with the CFS roller spreading the crop out and the rotor flights bringing the edges in, again, this all contributes to a more evenly filled load.
The 840mm diameter feed rotor features a helical pattern with Hardox tips. These can be replaced with fresh weld-on tips.
Knife bank
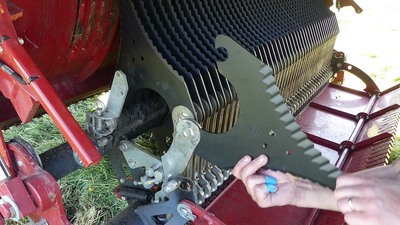
From this year, both the 01 and 02 will get the firm's new Exact Cut knife bank, featuring 44 knives for the 02 and 45 for the 01. This provides both machines with a theoretical chop length of 35mm. As with all forage wagons, quality of cut always depends on how the crop is presented to the feed rotor and knives. In our case, just from mowing with a mower/conditioner and raking three in to one, with the central swath effectively left untouched by the rake, chop quality on the whole was good. The test farm certainly had no complaints.
Stone protection on the knife bank has been well thought about, which sees rubber ‘knuckles' used to allow the knife to completely ‘trip out'. This is opposed to many systems which use spring pressure. With these systems, although the knife is allowed to move backwards out the way of an object, the constant pressure from the springs means the object rides all the way up the knife, often resulting in broken knife tips.
Strautmann's complete trip out system avoids this riding effect, meaning knives stay in better condition for longer. When a knife does trip out, if the crop is light, it will return straight back to its position. Failing this, a brief pause in work will see it return, or you can just keep ploughing onto the headland, where it will then have a chance to return. When a knife is tripped out, an alert shows on the control terminal.
Knives are also double-edged, allowing you to spin them around and use the other side. They are also very easy to get in and out, and the whole knife bank can be adjusted closer or further away from the chopping rotor, adapting to knife wear. It is a bit like adjusting a concave on a forager, as the knives wear.
In addition, there is also a lot more space under the knives now, allowing debris to fall through and avoid building up.
Door
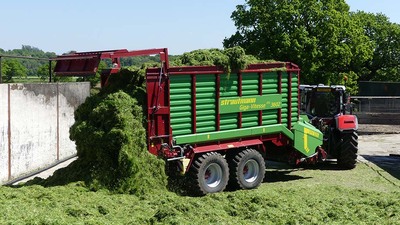
At the rear of the machine is a proper locking back door. According to the manufacturer, this is more reliable on this size of machine than up and over canvas-based doors. Full metal doors also add to the wagon's structure and strength.
When opening, a clever hydraulic ram system sees the door lifted vertically off the locking mechanism, before it is opened outwards/backwards. When closing, this is repeated in reverse, with the rams pulling the door down into the locked position.
Integrated into the door are LED road lights, which feature ‘Knight Rider-style' indicator lights. Working lights can also be programmed to come on automatically, when reversing at the clamp, for example.
As an option, the machine can be specified with a rear, side discharge conveyor, useful for zero grazing situations.
Tyres and running gear
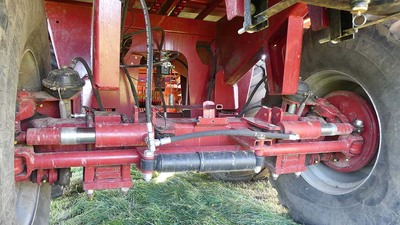
Underneath the machine, the Giga Vitesse rides on 710/50 R26.5 tyres as standard. Larger and smaller tyres can be specified, but the manufacturer says it was designed specifically with 710 tyres in-mind.
Wheels and axles are mounted on a sprung bogie chassis. Its pivot point is below the axles, which makes the machine easier to pull on softer ground, according to the manufacturer. There is the option of hydro-pneumatic suspension, but the uptake of this is very minimal, says the manufacturer.
Axles are also pre-stressed, to take into account the expected load, which look slightly bent when the machine is empty, but straighten out when loaded.
Active and passive rear wheel steering system options are also available. Ours came with the latter which did a fine job of maximising the wagon's manoeuvrability, especially around the yard. It also features an automatic locking system, which is activated when the wagon detects a reversing motion.
This is a great feature and provides one less thing to think about when using it in the field, such as when needing to shunt backwards in a tight corner. You can also programme the rear axle to lock in certain situations, too, such as when the emptying mode or when the road mode is selected.
Load-sensing air brakes and/or hydraulic brakes are optional and most greasing is via banks.
Filling system
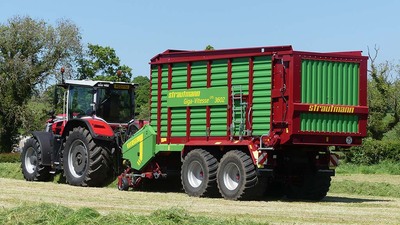
During filling, crop is pushed vertically up the headboard. At the top is a pivoting flap which holds the crop as vertical as possible, to help achieve an even fill. Integrated into this flap are moveable tines. These tines act as sensors which tell the floor when to move, if used in automatic mode. As the tines are pushed upwards, the floor moves in proportion.
Load density can then be altered via the Smart 570 control terminal in the cab and on the go; the greater the density, the less the floor will move to get more load squeezed in. For really wet stuff, this can be dialled back to 20/30 per cent. For us, in fairly dry conditions, we had it set around the 75/80 per cent mark. The main limiting factor is the tractor's power and what it can handle.
It is a system which works well, resulting in a pretty even load from front to back. When the load hits the back door, you then have three seconds to manually move the floor a bit further, allowing you to pack more in.
Floor
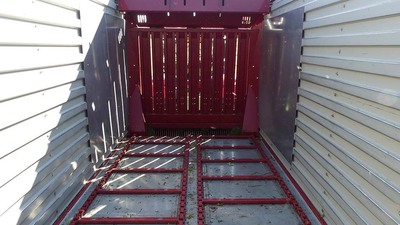
Unlike many forage wagon manufacturers, Strautmann has steadfastly avoided going down the sloping floor route. It says you get a better feed of crop into the wagon without it, with a more straight line flow of crop upwards, which is where you want the crop to go, not backwards into an already compressed crop. This puts less load on the chain floor, it adds, and keeps the pressure on the rotor, making the machine easier to drive.
From a maintenance point of view, this also creates more space under the front of the wagon to get at the knife bank. And when the drawbar is raised, there is plenty of room underneath. This said, you could also argue that Strautmann needs this space because it does not have a fold-out knife bank. Again, the manufacturer counters this, saying that a fold out bank just adds to a machine's complexity, and that its system is simple and reliable.
It is also not interested in automated sharpening systems, preferring to have a decent knife protection mechanism which extends overall wear rates.
On 02 models, a steel floor is standard, as are flat link chains. For greater reliability and simplicity, the firm has gone back to manual chain tension adjustment, done with screws underneath the wagon.
To protect the floor chains when emptying, the two-speed left and right floor motors at the rear of the machine start in a low speed. After a few seconds, you can then activate full emptying speed, unless it still detects too much load on the chains. For the most part, the wagon will normally let you press the ‘fast forward' button after a few seconds, without interfering.
Control
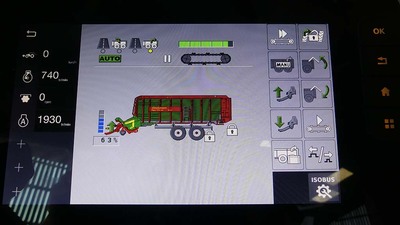
New Muller electronics are a feature on 02 models, which brings with it the new IsoBus Smart 570 control terminal, external buttons for drawbar adjustment and knife bank control, and automatic drawbar levelling.
Controls are really self-explanatory and easy to use, thanks to four automatic modes to step through as you use the machine; road to field, loading, road to clamp and unload modes. Simply select the right mode for the right situation.
Each mode can also be tailored, allowing you to pre-programme certain features to come on or off with each mode selection, such as lighting, rear axle locking and hydraulic lock-out.
When each mode is selected, the drawbar also puts itself in the correct position; low for filling, level for transport and high for emptying.
We tried both the machine's own control terminal and running it through the tractor's terminal. In both instances, what is displayed on the screen is identical, making it easy to switch from one to the other. If your tractor is capable, you can also assign some of the wagon's functions to assignable buttons on your tractor.
The wagon's own control terminal is also good to use, allowing you to either tap the icons on the screen or use the adjacent blister buttons. The latter are good for when on the move, allowing you to feel for the buttons without looking.
Verdict
Overall, for customers weighing up forage wagon options, the many different design attributes of wagons on the market, including our test machine example, certainly provide plenty of food for thought.