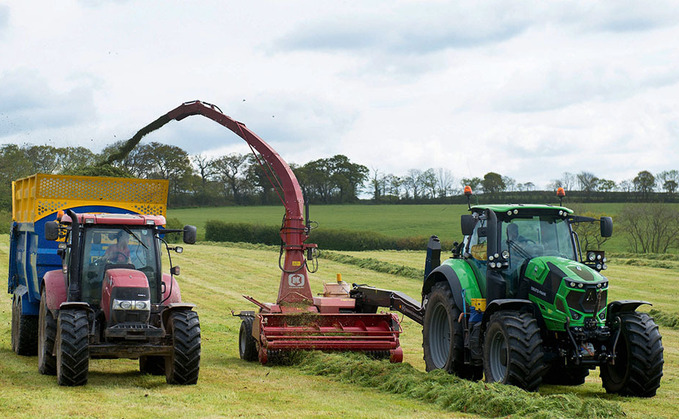
For one contractor, offering a precision chop service is possible because of the use of a trailed forage harvester.
The trailed forage harvester has for a long time been the preserve of the farmer taking forage production in house, with a relatively low-cost machine.
However, in recent years sales of the tractor drawn chopper have slumped, now barely reaching into the teens for machines sold.
PG Isaac and sons ran self-propelled forage harvesters as recently as 2015, but as owner Allan Isaac and chopper pilot Peter Fry explain, the decision to revert to a trailed setup was ultimately an easy one.
The company chops up to 600 hectares (1,500 acres) of grass each season, often on steep and challenging terrain, says Mr Isaac.
The first issue with this is getting trailers across the slippery slopes, made harder by the large capacity trailers needed to keep a self-propelled machine running at its optimum.
In contrast, with the trailed setup, smaller tractors and trailers can be used to ferry grass from the field to the pit, often owned by the farms the company services.
Mr Isaac also says harvesting in the South West often goes ahead when ground conditions are less than ideal, but the grass and weather are ready.
This prompted a number of farms to consider the impact on compaction and regrowth the self-propelled harvester caused.
Reacting to this, Mr Isaac decided the lighter and nimbler option of a trailed forager would suit the area better.
Self-propelled
Likewise, Mr Fry says driving the self-propelled machine around the narrow and twisting roads of the area was a difficult job in itself, whereas with the trailed setup, the job of moving from farm to farm is far simpler, due to its overall narrower width of three metres.
It has also enabled them to take on contracts for farms that traditionally would not have been accessible.
He adds that in the field the 3,600kg machine is also much more stable, as it is lighter and the centre of gravity is much lower, with a wide wheelbase to match. Its 430mm tyres keep it afloat in damp conditions. Up front is a 214hp Deutz-Fahr 6215 TTV, which provides plenty of power when needed, according to Mr Fry.
Often his customers buck rake themselves, so having a steady stream of crop coming into the clamp ensures plenty of time to consolidate the pit.
With the output of the self-propelled chopper and the need to keep it running at capacity to justify its existence in the fleet, farmers were quick to comment that they could not keep up with the amount of grass coming back to the pit.
Mr Isaac says that the new trailed setup - providing the grass is picked up before any inclement weather comes in - means his customers are far happier with this method.
The forager's 2.65m pick up keeps the 720mm-wide crop intake rollers fed with grass from the company's twin rotor rake, which gathers 10m into the swath.
While hectares per day may not be record breaking, typically 25 to 40ha, customers are happy about the quality of silage which is being made, says Mr Isaac.
Taking care of chopping is a 720mm wide cylinder, fitted with 24 knives. These are arranged in lines of four, across six banks. The manufacturer says the redesigned cylinder has a greater airflow, increasing blowing capacity, something Mr Fry would agree with.
He says: "Grass is consistently chopped to 30mm, although we can theoretically go down to 6mm.
"The chopper rarely struggles to blow the grass into trailers, even in heavy, sticky first cut."
Having run a smaller JF1060 from new for four years, previous to the 1260 arriving this year, Mr Isaac says reliability was very good, with no major issues and servicing a refreshingly simple and low-cost exercise, compared to the selfpropelled machines.
Mr Fry says the old self-propelled machines could cost up to £7,000 to service each year, a hard pill to swallow on the acreage they cover.
In contrast, he says £1,000 goes a long way on the trailed machine,most of which is due to its mechanical simplicity and servicing is done in-house.
The only way of justifying the extra service cost was if the machine was doing more work, by harvesting maize at the back end of the year as well.
However, Mr Isaac says the demand for maize harvesting fluctuated considerably each year, making the job of budgeting for the year harder.
Focus
It was decided to pass the maize harvesting onto a neighbour and focus on the grass silage operations.
Controlling the forage harvester is simple with the in-cab control box, he says. All the major functions are controlled from here, including spout movements via a joystick, which is very precise says Mr Fry.
Sharpening the knives is also a simple task he says. A pto shaft in the machine is disconnected from the main drive, and connected to another shaft that is independent of all other moving parts and runs in reverse.
A sharpening stone is then pushed across the knives. This operation only takes a couple of minutes, according to Mr Fry.
Without the trailed forage harvester, Mr Isaac says he would have to seriously consider his contracting operation, as due to his location the larger grass harvesting equipment is totally unsuitable.
Being able to continue accommodating local farms with a valuable service is important says Mr Isaac, one that he is able to do with the dying breed that is the trailed forager harvester.
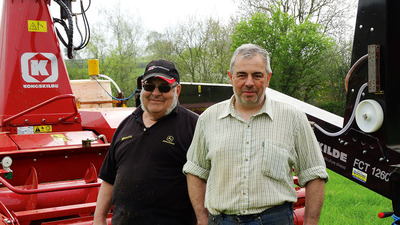
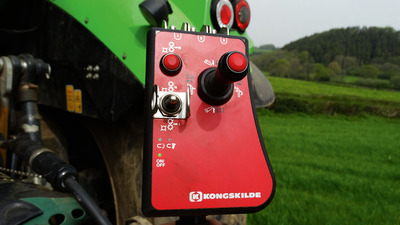
Verdict
Easier access to fields along narrow lanes, low overall weight and being able to operate with - usually farm-run - smaller tractors and trailers resulting in less of a compaction burden, are among the positives in favour of a trailed forage harvester.