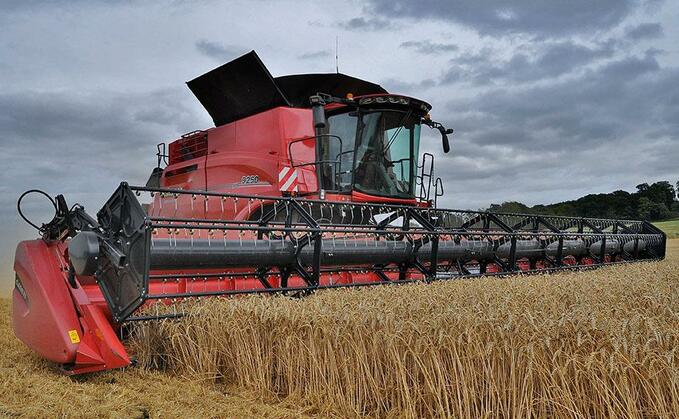
The new Case IH 250 Series Axial Flow combines will introduce advanced automation technology in 2019, but will it work in UK conditions?
To find out, Simon Henley attended an exclusive UK preview of the 9250 model...
Case IH's Axial Flow combine harvester has been with us for more than 40 years. By anyone's standards, such longevity is undeniable proof the single-rotor threshing system introduced by International Harvester in 1977 has stood the test of time.
By using a longitudinally-mounted rotor, design engineers were able to dramatically increase the threshing capacity of the combine without increasing its external dimensions.
This was, and remains, important as combines need to be driven down the road as well as transported by trucks and trains.
Another benefit of the singlerotor concept is its simplicity. The single-rotor design requires fewer wearing parts, which in turn means less maintenance and a combine which is easier to clean - still essential factors today.
Evaluations
Fast forward to today and, following our taster of the latest Axial Flow 250 Series' launch in Germany earlier this year, we caught up with the flagship 9250 in the UK as it underwent evaluations.
With a chance to run it alongside the current 9240 flagship, we were particularly keen to see if its new automated features made much of a difference, and what an experienced operator actually makes of the new machine
TEST FARM HOST: KEITH CHALLEN, BELVOIR, SCOTLAND
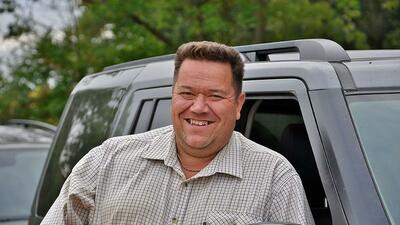
KEITH Challen is the farming director of the Belvoir Farming Company, a 1,400-hectare estate which surrounds Belvoir Castle in the county of Rutland.
Mr Challen, who grows about 1,100ha of cereal crops, switched from a Claas Lexion combine to a Case IH 9230 Axial Flow model six years ago.
He says: "The change to an Axial Flow combine was inspired by several things. For a start it was competitively priced and I really liked the simplicity of the Axial Flow design.
"The Axial Flow is a comfortable machine to drive. It has a longer feeder housing than the Claas, which positions the header further away from the cab. I personally found that because I was not constantly leaning forward to see the crop intake, I no longer suffered with neck ache all season.
Reliable
"Our policy is to change the combine every five years. The 9230 proved to be extremely reliable, so this season it was replaced with a brand new 9240 AFS model equipped with a 12.5-metre cutting table.
"This season the 9240 has proved to be more economical than the 9230, using about 5 per cent less fuel," says Mr Challen.
"We have also noticed engine recovery in heavy crops has been significantly improved. I will be very interested to see if the improvements CaseIH has made to the 250 Series will show a noticeable performance increase over the 240 Series."
A CHANCE TO COMPARE
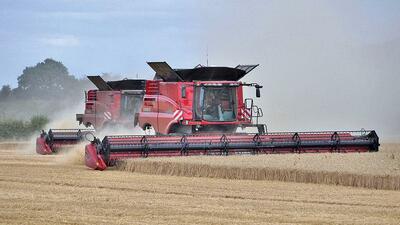
FOLLOWING the launch of the 250 Series Axial Flow combine range in Germany in July, Mr Challen was approached by Case-IH product specialist Paul Freeman, who had arranged for the new flagship 9250 AFS HarvestCommand model to be shipped to the UK for evaluation.
Although virtually identical in appearance, the 2019 Axial Flow 250 Series combine range introduces a melee of design improvements.
These include a more substantial feeder chain with heavy-duty cast steel slats, an upgraded feeder drive with a heavy-duty (175hp) transmission, a new two-speed hydrostatic transmission, higher capacity unloading augers, and remote (rotor) cage vane adjustment.
While these changes serve to improve the new combines' capacity, the trump card for the new models is the introduction of the optional AFS HarvestCommand system. This is an advanced combine harvester automation system which has been developed to improve the combine's output by up to 10 per cent. But does it work?
Case-IH demonstrator Ed Watson explains: "On this farm, we are working in wheat with the straw chopper engaged. Using HarvestCommand I can select one of four harvesting strategies, depending on the type of crop or the requirements of the farmer.
"In wheat, the objective is to keep the combine full to optimise threshing performance. In these conditions, a combine's performance is often limited by the power of the engine.
Overloaded
"If the engine is overloaded, the revs will drop, the rotor will slow down and threshing efficiency is immediately lost. We need to make the most of the engine's horse power to optimise threshing capacity without overloading the combine.
"Selecting the ‘maximum throughput' strategy enables the operator to establish an engine load target, which I have set at 107 per cent. This gives the engine boost system a 13 per cent horse power reserve, to accommodate fluctuations in the crop. This will give us the throughput, but we also need to control our post-threshing losses.
"One of the benefits of the HarvestCommand system is it allows the operator to quantify how much grain has passed over the back. According to the response, it will adjust itself to reduce the amount, or increase the combine's output to a level where losses remain acceptable.
"We work to a 0.5 per cent loss, which is established by getting out the combine and performing a visual inspection. Once a percentage is established, the HarvestCommand system will maintain optimum performance without increasing post-threshing grain," he says.
The HarvestCommand system is activated by a button in the overhead roof console so you do not need to use it. But, as Mr Watson explains, Harvest-Command is designed not to remove the skill of combining, but rather to help improve it.
"A man who has been driving a combine for 10 hours will naturally become fatigued. With the constant pressure of getting the crop in the shed, statistically even a seasoned operator is unlikely to change the combine's settings during the working day, even though harvesting conditions themselves may have changed."
AUTOMATIC FEEDING
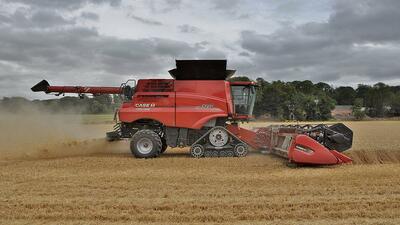
WITH HarvestCommand observing the combine's performance, changes in harvesting conditions are constantly monitored, so the potential for harvesting throughput losses are strictly controlled, if not eliminated.
But there is another feature on the new 250 Series combines which is equally important when it comes to optimising the harvester's performance.
Feed Rate Control (FRC), was introduced as an option on the 240 Series combines. As a concept it was a clever idea, however the efficiency of the system never reached its full potential, partially because it only monitored variations in load on the feeder drive.
On the new 250 Series, FRC monitors the load on the engine and, thanks to some new software with improved control logic, it is now an effective tool for maintaining a constant crop input without overloading the engine.
Mr Watson says: "FRC purely controls the forward speed of the combine. Using the perimeters we have set, it will try to achieve a programmed target speed, which is deliberately set higher than the combine is able to achieve, in this case at 7.5kph."
Guidance
The opportunity to get behind the wheel of the 9250 soon proved the merit of using the FRC in conjunction with the HarvestCommand system.
Guiding the combine towards the crop, you simply activate the guidance system and lower the header. As the guidance system takes over steering duties, you then press the FRC button on the joystick and push the lever all the way forward.
FRC now takes over, gradually accelerating the combine as it enters the crop.
MORE
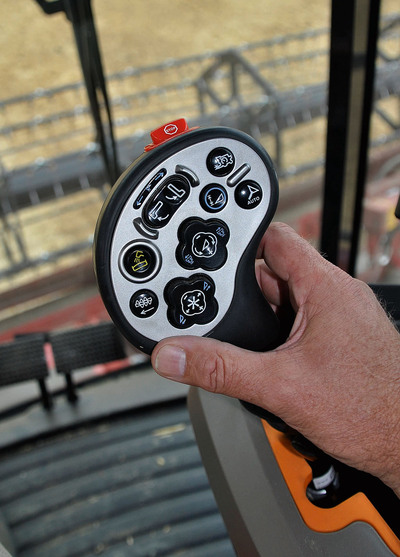
Working in this particular field, our rate of travel averaged 4kph.
Yet, as the combine worked its way through the wheat, the FRC system constantly fluctuated the speed, dropping down to 3.7kph where the crop was thicker and peaking at 5.5kph where the crop was patchy.
Mr Watson says: "If you watch the engine load monitor, you will see forward speed fluctuations occur in direct response to the engine load. A sudden increase in engine load reduces the forward speed - the FRC responds instantaneously, correcting the speed every few seconds. Trying to achieve this manually, even over a short period of time is almost impossible."
Confused
Switching off the FRC quickly proved Mr Watson was right. Using the engine load as a guide, a human operator cannot react to crop conditions as quickly as the FRC, although it is worth noting the system was momentarily confused by sudden bald patches in the crop.
What is important is that, with HarvestCommand monitoring the combine, the operator - no matter how experienced or otherwise - is left to cast a watchful eye over the vast ocean of crop passing into the feed elevator, and make sure there is nothing in front of the combine which could do serious damage to the expansive cutting table.
Verdict
In perfect conditions with an experienced operator at the helm, over an eight-hour day, it is unlikely there would be a discernible difference in output between the current 9240 model and the new 9250 Series equipped with AFS Harvest Command.
Unfortunately, here in the UK where perfect conditions rarely exist, seasoned operators are increasingly harder to find and eight-hour days are for people working in offices.
In the big picture, it is not difficult to see why advanced combine harvester automation systems, such as the Case IH AFS HarvestCommand with FRC, are necessary for taking combine efficiency to the next level, because they really do work.
Driving a combine of this size, nobody can continually concentrate for 14 hours, says Mr Challen.
"I believe systems like HarvestCommand, when used with modern guidance systems, are increasingly necessary to improve combining efficiency.
"Changing weather patterns have meant the UK has experienced more extreme weather in recent years. The additional pressure of gathering the harvest combined with the cost of these machines, demands they are working at maximum output throughout the harvest season."
Sold as an option, AFS HarvestCommand adds about £15,000 to the cost of a 250 Series combine.
Assuming a residual value on the system of £5,000 at the time of trade-in, over five years on a farm harvesting 810 hectares per year, the cost of HarvestCommand equates to about £2.50/hectare.
Mr Challen says: "The cost of this kind of technology is virtually self-funding on a farm of this size. In my mind, HarvestCommand provides a level of technology necessary to maximise combining efficiency in today's farming environment."