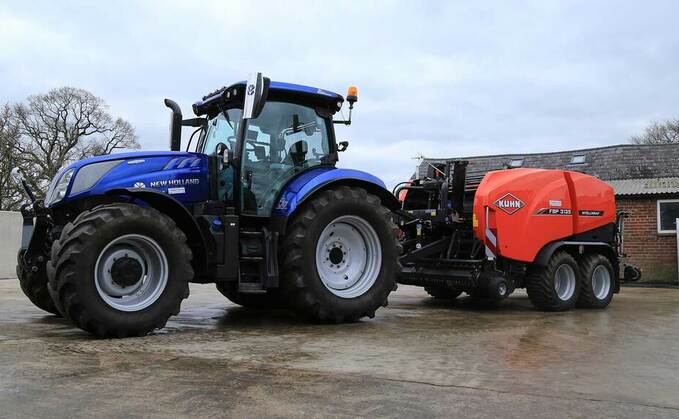
With more customers requesting a one pass baling and wrapping operation, one Cheshire contracting company took the plunge on Kuhn's FBP3135 combi-baler. Alex Heath finds out how it has been performing.
For Rick and Will Venables of J and JA Venables and son, the saving on wrap alone is reason enough to justify their purchase of a Kuhn FBP3135 combi-baler, which they have run for the past two seasons.
Few machines split opinion like the brand of combi-baler to go for, however, the brothers from the 33 hectare Holly Tree Farm near Macclesfield, reckon their new baler is mixing it with the best, boasting a range of features, previously not seen on the market prior to its launch in 2017.
Rick explains: "We farm a total of 250 acres made up of our own land and rented in. Initially we had a Kuhn FB2135 baler to service our own needs. However, we started a bit of contracting work and soon began to grow our customer base. They were happy with the weights in the bales, but being a stand-alone baler, another contractor had to come in with a wrapper to finish the job. Customers started asking if we could do the whole job, but we were reluctant to buy a wrapper.
"At the end of the of the 2018 season, we started looking at our options, researching what was on the market narrowing our list down to the McHale Fusion, Vicon FastBale and the Kuhn. We had Kuhn's new combi-baler on demo from local dealers Malpas Tractors and were impressed with the speed it baled, the density of the bales and the wrapping process."
The brothers explain the quality of the bale is paramount to their business, both for retaining customers and taking on new ones.
Rick says: "At the end of the day, consistency of bales is one of the most important things when baling for customers and with the Kuhn, we think it is hard to beat. This includes even weights and ‘squareness' of the bales, making sure both shoulders are as full as possible. The baler lets me know where it is short on grass and directs me to the side of the row to fill up the left or right, giving a more even bale.
"Weight wise, we get just over a tonne in most silage crops into the four-foot bale, 650-850kg in haylage and 300-400kg in hay. The amount of material it packs into the bales is impressive and helps the bales to retain their shape when stacked. We have never seen any bales slump after stacking."
The usability of the baler scores highly according to Rick, with automatic features incorporated into the baler's computer.
He says: "The baler is equipped with the 14 knife Opticut system. We bale with knives engaged for half the jobs we do. One feature I really like is when the bale gets to 90 per cent of its final diameter, the knives disengage from the rotor which allows a full rotation of unchopped grass to be put around the outside. This really helps to bind the bale together and when you take the wrap off, the bales do not fall apart, like they would if it was all chopped."
While Rick spends most of the time operating the baler, Will is responsible for rowing up ahead of it. A lot of their work being in the heart of Cheshire is dairy based and frequently in paddocks surplus to farm's grazing platforms.
Will says: "A lot of the paddocks we do are small and can be rough from hoof prints. You just have to watch the pickup to see how smoothly is travels and hoovers up the grass. It rarely blocks as the distance from the pickup to the rotor is so short; there is always a constant flow of crop forcing its way in."
However, the pickup is one area Rick would like to see a change made. "The pickup wheels can be moved up and down to adjust the height, but they do not swivel. While we have not seen any problems with them being fixed in direction, I would prefer to see swivelling castors used for piece of mind when baling headlands."
When the demo baler came, Rick says it was running alongside a McHale Fusion. "The Fusion was slightly faster up the rows, however, the Kuhn was putting one bale per row out less, indicating to me the bales it was producing would be heavier. They were also more consistent in size and shape, which made up our minds."
The wrapping system and the way it uses wrap is the baler's piste de resistance, reckons Rick. The baler is equipped with film on film technology that applies film instead of traditional net wrap. And where it differs form other film on film balers on the market is that it uses standard 750mm rolls of wrap, rather than special full width rolls, making it easier and more convenient he says.
"The wrap used to bind the bale is the same as is on the wrapper. Two rolls are used, pre-stretched before binding, resulting in a slight overlap in the middle. We put three layers of wrap on the cylinder of the bale in the chamber, which is enough to hold it together. I also think the bales store better because of this, as the air is squeezed out of the bale in the chamber and the film put on in the wrapping process sticks to the film from the bind process much better than it does to net wrap. We get about 130-140 bales out of a pair of rolls for the binding process," says Rick.
"We then give five layers of wrap from the wrapper, so the cylinder effectively has eight layers on. The wrapper saves us film as it is Kuhn's 3D system. Its starting position is the same as a normal table wrapper, putting a revolution's worth of wrap on the flat side of the bale. Then, the rolls and dispensers rotate 90 degrees, so they are presented to the bale horizontally rather than vertically. The bale rotates on the table and the wrapping arms slowly rotate, covering the cylinder. The rolls then revert to vertical position and finish the flat sides of the bales."
The system is very effective agree the brothers, with about 48 bales wrapped per pair of rolls. Will says: "The wrap is where it is needed, on the round part of the bale, which is where it is most vulnerable. In instances of pinholing, the ingress of air is minimal, little mould forms in the bale."
Switching over to net wrapping is a simple procedure for straw baling says Rick, however, he adds that they have tried using film as a protective layer for straw stored outside.
"When baling straw in the heat of the summer, the film binding is not ideal as the wrap becomes too thin, however, we tend not to bale much straw and can arrange to bale at night when it is cooler if needed," he says.
Overall, the pair have been impressed with the quality and consistency of bales produced from the baler and hope to grow their customer base off the back of its performance.
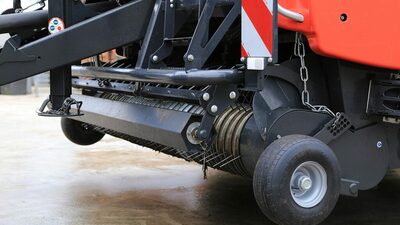
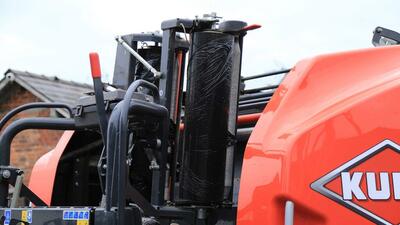
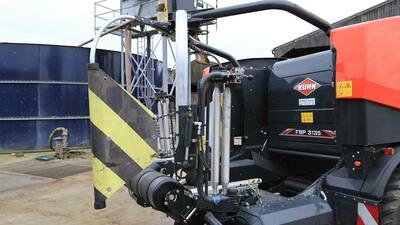
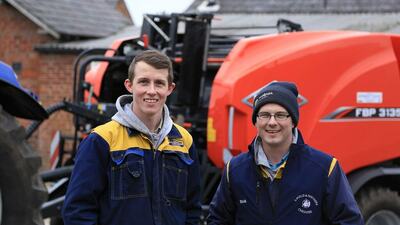
Verdict
Rick reports the baler has so far been very reliable with no major issues. Bale ejection from the chamber to the wrapping table is good he says. With two kicker arms transferring the bales, even if a bale is not bound properly, it is propelled onto the table with little fuss. He adds that the controls at the rear of the bale also make it easy if a miss bind does occur, able to sort it out with full visibility of the chamber. The only addition he would like to see on his baler are more work lights, both on the wrapper and under the panels, to make maintenance easier at night.
Rick says his best day piloting the baler saw 600 bales made, contributing to its workload of 7,000 bales per season. He anticipates the baler will be on the farm for the foreseeable future and hopes to grow his customer book off the back of it.