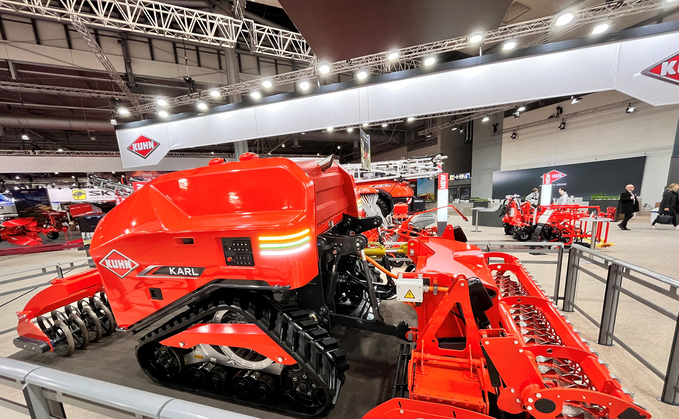
Kuhn's Karl concept is an diesel hybrid autonomous tractor designed to work individually or as part of a team of machines.
Karl uses a 175hp Volvo hybrid diesel-electric drive, which is combined with high voltage take-off to power implements. Kuhn has remained reserved on details, other than saying the design is a fully functional concept that has been developed to work alongside existing machinery to increase infield productivity, and has the ability to function as part of a team of multiple units. Drive is through a pair of rubber tracks with front and rear linkages to allow multiple-pass implements to be linked with each power unit. Lift capacities of the linkages are rated at five tonnes for the rear and 3.5t for the front.
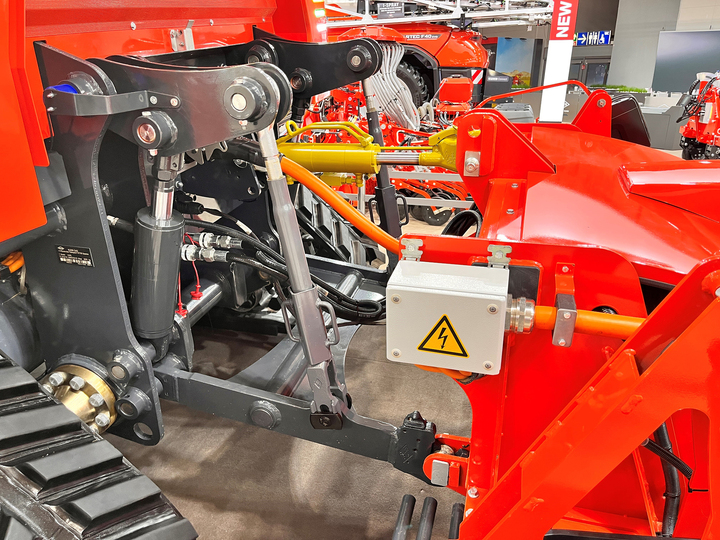
Shown at the event, a modified HR2520 2.5-metre wide power harrow - specifically developed for Karl - was linked to the machine, with the implement using an electric drive as a pto replacement, and several additional sensors to monitor the working characteristics of the cultivator, which can be fed back to Karl or the operator to make adjustments.
Control of the unit will be through a mobile or desktop interface, with transportation of the complete machine between fields achieved using a low-loader.
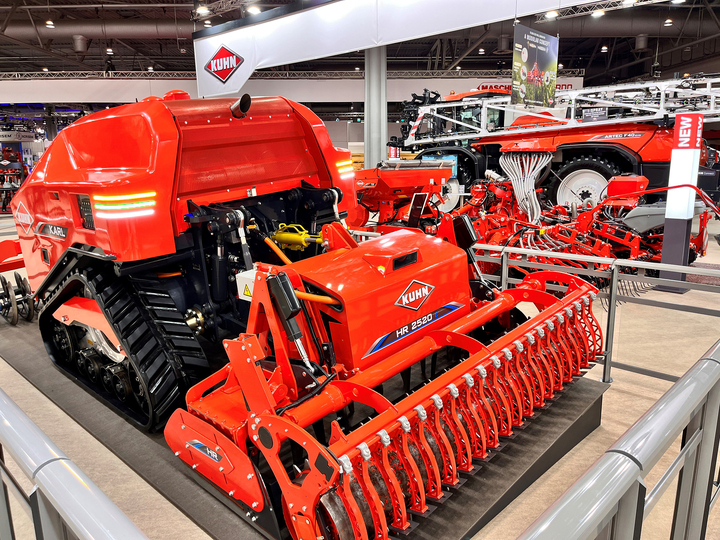
Kuhn says that the control and object detection system used operates using similar technology and principles to the Aura autonomous total mixed ration feeder, which was launched to a limited market area in 2022. This system used a combination of GPS mapping, RTK positioning, radar and lidar to determine its relative position and detect objects moving around it. Aligning to the requirements for all autonomous vehicles, the three coloured lighting bars on each corner are used to alert bystanders of its state of operation, and visually signal if the machine has encountered a problem.
In terms of its somewhat pastoral name, Karl is not an acronym for an aspect of Kuhn autonomy, but simply a name which is easily pronounced in multiple languages.