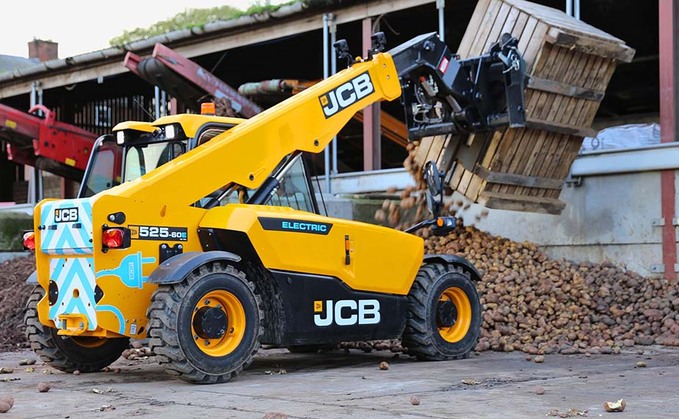
As the buzz around electrification of farm machines marches on, the latest manufacturer to join the fray is JCB with its 525-60E telehandler. To see what the battery powered loader is capable of, Alex...
As the buzz around electrification of farm machines marches on, the latest manufacturer to join the fray is JCB with its 525-60E telehandler. To see what the battery powered loader is capable of, Alex...
2021 John Deere 6155R Ultimate Edition Command