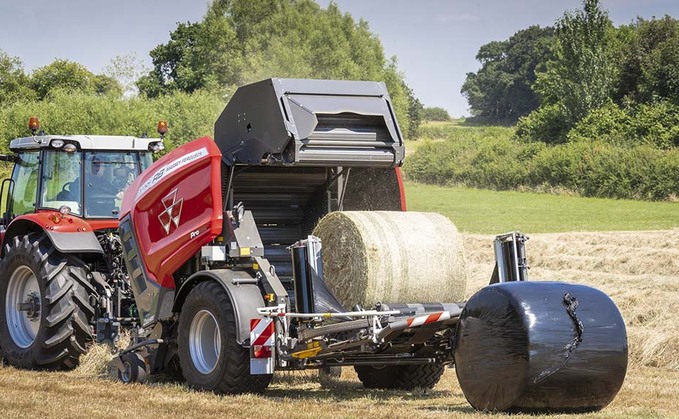
Industry developments are looking at ways to make forage conservation more sustainable, but do not expect to see biodegradable wrap any time soon. Jane Carley reports. With the drive to reduce single-use...
Industry developments are looking at ways to make forage conservation more sustainable, but do not expect to see biodegradable wrap any time soon. Jane Carley reports. With the drive to reduce single-use...